By Paul Wiseman
Overwatch Solutions owner Brandon Crate likes catching perpetrators on camera. Cognite’s Global VP of Partner Success, Prabu Parthasarathy, loves consolidating and freeing corporate data from siloes. ATI’s (Automation Technology Inc.) CEO, Cooper Etheridge, is dedicated to being able to relieve pipeline pressure to avoid problems.
All three employ technology to automate and streamline those things for clients.
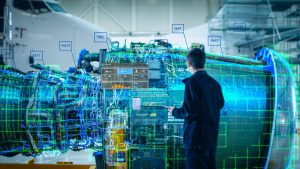
Widespread retirement of personnel from the oil and gas field has created a huge knowledge gap. Cognite’s Parthasathy sees AI and
its ability to analyze massive databases as an option for helping new people bridge the knowledge gap.
Prevention, the Best Medicine
Brandon Crate would much rather his automated-camera-based security system would deter crime than immortalize it in digital form. That’s why his favorite system version to deploy is one with bright, flashing lights in bold colors—so anyone contemplating a crime will think differently, at least about the site in question.
Crate explained, “We’re trying to prevent crime, and just by placing these cameras there—they’re not made to be hidden, they’re an overt camera, and we want people to know that they’re cameras.” To that end, the company installs what Crate calls “blinky lights.” The colors of the light can be chosen by the client, and they can flash or be constant. “These are the same lights we use on the police cars, on the push bumpers.”
Across his years of solving crimes in Oregon, Crate reviewed hours of surveillance camera recordings.That experience taught him a great deal about camera placement and the exact data the police department needed in order to further the investigation. Crate used that knowledge in establishing the company in August of 2022.
Since then he’s learned that the blinky lights do indeed have an effect. “We’ve seen crime reduction of between 20 and 50 percent in certain areas after just physically putting them in.” But even if the actors do commit the crime, “Then there’s documentation, that’s another facet.”
Documentation Is the Next Level
For the benefit of remote oilfield locations that lack dependable cell or satellite service, the company’s units are self-contained, recording everything internally. That way there’s certain to be a record of any event, when needed, that won’t literally get lost in transmission.
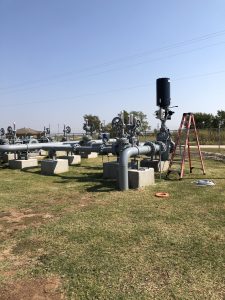
In midstream, when a leak occurred, it used to take a human being to go to a valve and manually shut off the flow. Not any more. ATI has equipment now that does that automatically.
That same remoteness may also mean that a company doesn’t become aware of a theft until an unknown period of time after it happens, Crate pointed out. “If somebody steals something from, let’s say, an oil rig or something like that and you say, ‘Hey, I don’t know when this occurred—I think they got a couple of pipes or a few barrels of crude and that’s all we’ve got’—that’s exactly how the police report’s going to read.” He added, “If there’s no evidence, no police department’s going to work it,” because there’s not enough evidence to go on.
But with a video of the license number (one of the Overwatch systems reads license plates), things are suddenly clearer. And while the license number is pure gold, even without it an ID can be made on the make, model, color, and any scratches or other distinguishing marks. The time, date, and a view of the stolen items will also be available.
Systems can record constantly or they can be triggered by a motion detector, which can differentiate humans from animals, motorcycles from pickup trucks, and so forth. But over the years, Crate has observed that an action can sometimes occur just outside the motion detector’s range but within the camera’s vision. So, where possible, constant monitoring may be the most sure bet. For locations where remote communication is available, alarms can be set up to text or email people on a recipient list when the system detects a likely problem. Night vision cameras are also an option.
With a wide variety of configurations and options, Crate said no two systems are exactly alike, the exact design depending on what the site requires to satisfy the customer’s plan.
With oilfield theft on the rise, Craft feels remote, automated monitoring is a valuable prevention and detection tool.
Gathering and Liberating Formerly Siloed Data
The digital age has come about in stages, it seems. Merely collecting data is a start, but, notes Prabu Parthasathy of Cognite, getting all that data together where everyone can access and apply it toward decision-making—that’s another story. The industry term for this kind of separation is “siloing.”
The company’s Cognite Data Fusion (CDF).product is designed to securely connect these siloes so management and staff in the various departments can become more efficient in both planning and operations. They can do this without spelunking through a labyrinth of siloes every time they need to know a purchase date or the date of the most recent PM.
“So we bring that information together and connect it all together in what we call an industrial knowledge graph.”
Using a single oilfield pump as an example, he pointed out that its purchase data and manufacturer specifications can be in one system in accounting, with maintenance records on a computer in the operations department. Anyone wanting to match the two would deal with separate systems and possibly slightly different names for the same pump. That could make it difficult and time-consuming to verify the information
To solve that, “We automatically recognize that this is the same pump that’s mentioned in all these different places, so that it’s all connected. And when an SME [subject matter expert] in a company wants to consume this data and understand something about the pump, they can go to this one place and pull all that information together and see it,” said Parthasathy.
That’s what he calls “liberating the data.”
Then, “Once you liberate the data, now you can add a lot of value by layering applications on top, tech domain knowledge on top of it, because that’s
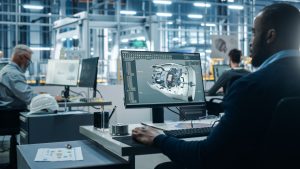
“Siloing” data is a common practice in data management. Cognite, with its “Data Fusion” product, helps to link those silos to unify the existing data.
what an SME does. They look at this information, they’re adding their knowledge to it and getting insights and value from it, and using it in the day-to-day function. So we build applications in that space as well, and we partner with companies to provide that domain specialization,” he added.
Practical Applications in Failure Analysis and Prevention
With a typical E&P company monitoring anywhere from 200 to 1,000 wells with a small crew, their people can be overwhelmed with more data than they can manage. And if production goals are not being met, there can be dozens of potential issues for that small staff to sort through. Is it a maintenance issue? Is there a pipeline issue? “That is a complex decision making process,” he said. First, the problem must be identified. Then, “You have to optimize which technician goes where to fix a problem.” Optimizing that process, getting the right technician to the right job with all the parts and supplies needed, is something the AI can contribute to.
The Future
The issue of “information retirement”—experienced oil and gas people retiring or changing fields, without the normal progression of being able to train new people, is creating a huge knowledge gap. Parthasathy sees AI and its ability to analyze massive databases as a mitigating factor—an option for helping new people bridge the knowledge gap. “Generative AI can hugely help because you can mine the information that you’ve created over the last 20-30 years of working in these assets,” and the associated reports and procedures. “All of that is complex information from which you can mine knowledge.”
He added that “We are able to create insights from the data without actually exposing clients’ data to the LLMs, which is one of the risks that people talk about.”
LLM is short for Large Language Model, part of the sampling of public data that informs and provides context models for generative AI like ChatGPT.
Safely Addressing Pipeline Leaks—Remotely
For ATI’s Etheridge, pipeline safety and leak mitigation is the key.
In the Permian Basin, pipelines—on a well site or cross-country—carry liquids and gases that are simultaneously valuable and dangerous. In neither realm is it a good idea to let those products loose. But here, too, are constraints of remoteness and distance. In years past, an overpressure situation could cause a rupture or other issue without being detected for days, causing damage and loss—or, a small army of people would have to be paid to constantly drive by. Even in the latter scenario, there were gaps in observation that could allow unobserved issues for hours or days at a time.
To that point, he said, “There have been instances where a pipe leak occurred and a fire started, and it took a very long time for someone to drive to the closest valve and shut it by hand.”
Founded in 1995, ATI’s original purpose was to build and install actuators that had the power to quickly and easily operate the large valves that control pipeline flow, Etheridge said. He explained, “The actuators are sometimes the muscle behind the system.” For him and his company, “Safety is a huge aspect of it,” especially regarding emergency shutdown valves, or ESDs. “You really have to know the actuator is going to shut” the valve.
There are actually a couple of ways to operate a valve. Human muscle is the most basic, but it requires those muscles to be onsite. Actuators operate valves automatically without human presence. In the wide open distances of the Permian Basin, this is essential.
In dry gas pipelines (little water or other liquids), pipeline gas pressure can be used to power the actuator. In recent times, Etheridge noted, “There has been an increased need to find other ways of operating the valve. Either the pipe has natural gas liquids, it contains crude oil, or it’s natural gas, but not dry enough.”
A second driving force is the push to reduce methane emissions. Electricity is one option, he said, but here again the remoteness of the Permian means many wells are beyond the grid’s reach. “So instead of using the gas in the pipe, we use nitrogen bottles or electricity if it’s available. Or just the sun. So you have to use nitrogen bottles or the sun. Nitrogen bottles have to be replaced. The sun doesn’t,” he said.
For remote monitoring, computer systems can be set up to detect leaks and trip the actuator. Or there’s a purely mechanical option, Etheridge pointed out. “For example, a system can use small tubing and a differential pressure gauge to physically sense a rapid increase in flow, which would be un-ordinary enough to indicate a leak. This can trigger an actuator to close.”
He noted that most customers for the company come from midstream clients as well as producers.
In the oil patch, remote monitoring is more remote than in most other fields not involving an expedition to Mars. So clear, accurate, and accessible data on conditions and processes is of great importance. Every day, it seems, technology is getting better at doing exactly that.
Paul Wiseman is a freelance writer in the energy sector. His email address is fittoprint414@gmail.com.