Artificial Lift in the 21st Century is a technological marvel. Three experts discuss the latest breakthroughs.
As electric submersible pumps (ESPs) and various assortments of gas/plunger lift designs continue to benefit from automation and other technology, one might be tempted to think the iconic rod pump is being left behind. And while remotely controlling a rod pump presents some challenges compared to the others, even there new advancements—both in pump design/materials and in monitoring and control software—are boosting performance. Here Liberty Lift, Production Lift Companies (ProLiftCo), and Baker Hughes provide updates on a variety of lifting systems.
Rod Lift: Staying in the Game
The pumpjack is going places, but it’s not going away.
“Rod lift in general has changed a lot over the last five years,” said Trevor Evans, who is VP over most types of lift systems for Liberty Lift. Bigger units and longer stroke lengths for pumping units on Permian Basin unconventional wells are becoming the norm, he pointed out. One reason for the changes is the increasing gassiness of wells. However, another is the fact that horizontal wells are better controlled by using parameters unique to unconventionals instead of relying on numbers based on their older vertical cousins.
Almost all unconventionals begin life with ESPs, producing 2,500 to 3,000 barrels per day, for up to a year or more. But as they pump the well down to around 300-500 bbl/d, fluid levels drop and gas content rises. “And those ESPs do not like gas,” he said, “so they start burning up quicker,” dropping from a life span of six months-plus to less than three. At that point, when replacing a pump costs anywhere from a quarter to a half million dollars, operators decide to switch to rod pump because the latter handles gas better.
He has observed that when oil prices are higher, many E&Ps want to accelerate production in order to maximize profits during that price window. That can cause them to leave the ESP in as long as possible. Maximizing production has also led Liberty to increase pump size and stroke length.
While five years ago the most popular stroke lengths were 168” to 192”, Liberty lift is now seeing averages of over 200” becoming more common, even reaching to and beyond 306”. Evans said the company has developed what is currently the longest pump stroke, 416”, which can move 700 bbl/d, often at 60 percent pump efficiency.
Even with that, rod pump operating systems are challenged by the gyrating production dynamics of today’s wells, Evans explained. “A lot of these wells will change their dynamics hourly as the reservoir changes, so optimizing rod lift today is a lot different than it used to be.” He added that, “These reservoirs are kind of living, breathing things.” Due to gas slugging, a rod pump may alternate between 80 percent efficiency and 50 percent when the gas builds up. Even various wells on the same pad may perform very differently, he noted, adding, “It makes it challenging and fun.”
Balancing Act
Evans’s goal is like that of many in the industry—to balance pump operation at the perfect line between maximizing production rates while protecting pump life. With the aforementioned dynamics of today’s wells, he says it’s necessary to rethink rod pump variable speed drives (VSD). VSDs designed for vertical wells do not calculate pump efficiency using horizontal well parameters such as inclination chains and deviation, “And they’re really guessing at pump efficiency.”
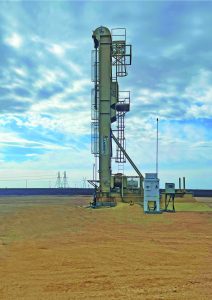
Manufacturer KWM builds these long stroke pumping units, also known as XL Units. The Automation/VFD is beside it, sporting the Liberty and Wellworx sticker on the box that looks like an electric panel. This unit has a stroke that is 366 inches or higher.
He said Liberty Lift is partnering with WellWorx to “build out the next phase of automation on horizontal wells, using it to process data and make really educated decisions.” Gathering consistent well data, as the conditions change throughout the day, will help programmers create a system that will appropriately adjust the system as often as needed.
Eventually, he sees AI making many, if not all, the necessary adjustments on its own. There is understandable reluctance on the part of operators right now, but he feels that in three to five years this level of automation will be more accurate and more acceptable—especially as M&A activity cuts staffing, leaving each remaining employee with an ever-growing number of wells to manage.
Other Advances
Improvements can come from all directions, not just from software, he pointed out. With gas locking, both ESPs and rod pumps can benefit from better gas separation, and Evans says his company is researching exactly that. While improvements may be incremental, he noted that even a five percent improvement would add up over time.
The company is also working with new formulas for rods themselves. Finding that the classic chrome is sensitive to the increased acidizing activity in unconventionals, they are looking at Brass Ni-Carb and other formulas to reduce corrosion and extend the unit’s life.
Automation for Plunger Lift, Gas Lift, and Their Combinations
For ProLiftCo’s Mike Swihart, automation is a “big deal, where you can do just about anything on your phone these days.” A single automation platform can connect more than a dozen wells, some up to two miles apart, with a home office located hundreds of miles from the field.
“You get constant trend data on what’s going on with plunger lift wells and plunger-assisted gas lift wells [among others],” Swihart said. ProLiftCo specializes in these kinds of low-energy-draw lift systems.
Automation like this is usually focused on what he called “higher-value wells. “We tell customers, if you’re going to put a plunger on a higher-value well, put automation on it to be able to watch it.” He also notes, “Any well that makes a little money is worth keeping an eye on.”
ProLiftCo staffers also monitor the data, alert for trends that might indicate a situation that either needs immediate attention, or might need it soon. When that happens, “We’ll contact the customer and say, ‘You’re missing some runs here,’ or, ‘It looks like your system went down,’ and see if they want our assistance,” Swihart said.
ProLiftCo staff members note whether the plunger ran every time it was supposed to run, and whether its runs were within the expected time frame, Swihart explained. “If it missed a run, we want to research—what happened there? It could be that, when you look at the trend data, the pressures, and the run times, we can say, ‘Oh, I could see that was about to happen, we could’ve seen that coming.’ So now we can make an adjustment to the settings and maybe get the well to recover on its own.” If in-person intervention is required, it can be done quickly, to limit downtime and maximize production.
Swihart notes that there is an upfront cost for installation, but that the system offers a significant net profit by reducing time-consuming site trips and its quick reaction time increases production. Energy and infrastructure costs are held down by the fact that the systems run on solar power.
His company offers to help producers because, said Swihart, many are less familiar with plunger and gas lift than they are with rod pumps and ESPs. In addition to real-time help, ProLiftCo also offers training in the office, through lunch-and-learns, and in other ways.
The same automation that provides ongoing well data also gives technicians remote control, he noted, “I’ve had clients call our field service people on the weekend and say, ‘Hey, we just had a ruptured flowline in this part of the field, can you get all our wells shut in over there?’”
Later, after thanking his own technician for fixing the issue, Swihart sometimes hears, “’It was nothing. I was watching football, I just got on my phone and I shut them all in within five minutes.’ And obviously, we can bring them back on, too. We can make remote adjustments on anything in the field.”
New Baker Hughes Tool Boosts Safety of Permanent Magnet Motors
The use of permanent magnet motors (PMM) to drive ESPs has risen in recent years, as PMMs can pack more power into a compact space while delivering more energy efficiency, among other advantages. But the tradeoff has been that those permanent magnets can generate their own power when fluid is forced through the attached pump when issues arise such as fluid fallback, well intervention, ESP troubleshooting, and ESP pulling or installation. The current created during these situations can be dangerous to personnel and equipment topside—and once the power flow starts, it may take hours to get it stopped.
The main preventive measures currently in place are procedural, said the company’s Senior Service Delivery Manager for the Permian ALS Operation, Jerrad Grisham. “That means you’re having to check for voltage generation at the surface,” he pointed out. The standard operation procedure [SOP] instructions just for checking voltage takes up three or four pages in the safety manual.
“Volt Lock represents a major advancement in safety for the Permian Basin energy sector,” Grisham said. “It eliminates hazardous voltage generation in ESP operations, and really showcases our commitment to a safer, more efficient field operation.”
With Volt Lock Baker Hughes wanted to add an engineered control that would supply a layer of protection in case of a procedural misstep. Grisham stressed that the Volt Lock does not replace procedural control operations, it only adds that mechanical protection layer.
The Volt Lock unit is about a foot long, a purely mechanical device, easily bolted on to the head of the motor. It provides an engineered control solution to prevent backflow through the pump from spinning the motor, which is what would generate dangerous voltage. This is only an issue with PMMs, not with traditional induction motors, Grisham noted.
It is designed to be installed with a Baker Hughes ESP, and when that pump is replaced, the new pump gets a new Volt Lock. The device is designed to be effective for the ESP’s entire run life. For right now, Volt Lock is only used with Baker Hughes equipment, but Grisham said there might be a future for selling the device for use across the ESP industry.
The new safety design is having a ripple effect on how producers choose their ESP motors, said Grisham. Having released the first Volt Lock units in early 2023, operators are seeing the unit’s success and its benefits in preventing unwanted power, so “We’re starting to see Permian operators now embracing the PMM technology with confidence, thanks to Volt Lock’s groundbreaking safety features.”
Some of that confidence has come from inviting potential buyers to the company’s artificial lift headquarters in Claremore, Oklahoma, for demonstrations and training.
With drilling costs rising and the future of leasing on federal lands looking iffy at best, producers are increasingly looking to maximize profits and production on existing wells. Even the staid and dependable pumpjack is getting a new look in that process.
By Paul Wiseman