The oil and gas industry follows a trajectory that mirrors the progression of the world. There has been the pursuit of prosperity, certainly. But apart from that, the pursuit of information has in itself come to carry great significance and the accumulation of information brings with it power. As the oil and gas industry has transitioned, at least in part, from a blue collar industry to a tech industry, its growing ability to gather information, cultivate it, and manipulate it for a specific purpose has been nothing less than a paradigm shift. O&G’s focus on information manifests itself largely in the form of automation.
Automation is not a new concept in oil and gas but one that is continually evolving and improving. What originated as solutions for specific problems has grown into a concept that can be applied throughout the industry’s entire value chain. The ways whereby automation has taken information and implemented it for particular purposes reveals a step change in the very methodology of oil and gas. This evolution has wrought a powerful tool that increases efficiency while driving profits, empowering consumers, and supporting livelihoods.
How It Works
The process can be seen on the local level just as on the macro level.
Consider the work being done by Nava Control Solutions. While servicing multiple industries, Nava Control Solutions additionally offers automation packages to the oil and gas industry, including commissioning services, PLC applications, and human-machine interface applications. According to Erick Mendez, Nava’s head of engineering, automation integrates into multiple areas of oil and gas with a focus on upstream production facilities. Controlling gas lift and monitoring well temperatures and pressures are challenges that impact production. Automation resolves these challenges, along with other factors, such as flow control and PLC programming going to process facilities and equipment.
“When you work on the automation side of oil and gas, you typically see two kinds of teams,” said Mendez. “You have the team that develops the programming and instrumentation design. Then there is another team responsible for commissioning, which includes all the people that put each automation component into service.”
Automation has emerged as a significant tool for improving production. It enhances the production process by achieving higher efficiencies. Tasks can be completed more quickly while manual labor costs go down. By automating processes and eliminating the need for a physical employee, human error can also be reduced.
“Humans are good at conducting certain tasks, but we make mistakes,” said Mendez. “Automation can do the work for you, and I believe if you create an excellent process and it is documented and standardized, using automation will make that process more efficient, and that will bring an increase in production at the end of the day.”
Automation Will Only Accelerate
Automation demonstrates quantitative value in the way it reduces workforce costs and enhances production to levels that generate higher profits. There exists, of course, the chance that opportunities for automation could reach a ceiling, thus flattening the profitability curve, but that remains an unknown and is likely a distant prospect at worst.
While the industry’s history is colored with stories of wildcatting and exciting improvements made in drilling and completions, automation has opened a new channel of increasing profitability—doing so through boosting production rates. Greater flow and output equals great production, both flow and output are highly receptive to automation.
Meanwhile, automation promises the ability to solve other issues that affect oil and gas. Emissions control has become as prominent of a focal point as flow control. Automation can be used to meet these demands.
“New system designs are growing increasingly tankless to avoid emissions,” said Mendez, “Additionally, there has been a movement away from using gas to operate valves. Automation solutions can be electrified to operate actuators.”
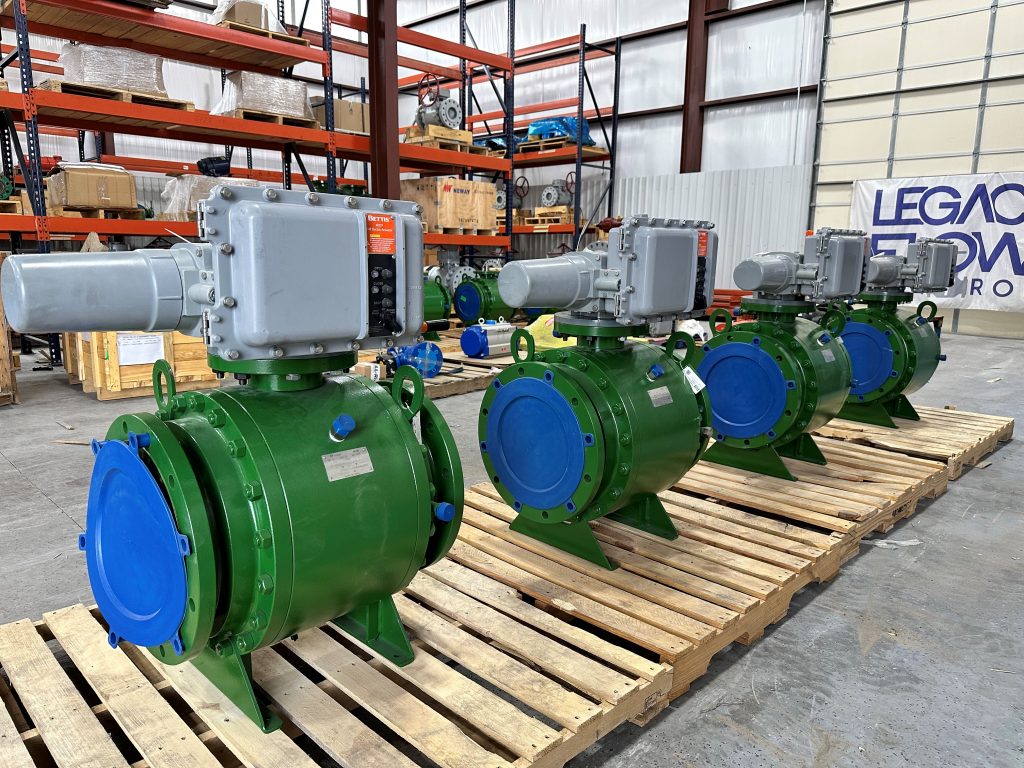
This is the direction the Basin has been moving for years: creating systems that can be operated remotely.
Actuators—Where the Action Is
Chad Brown has plentiful experience in valves and automation. As owner of Legacy Flow Control, he has led his company in servicing oil and gas customers with advanced manual and automated valve packages. Brown understands the critical role automation has played in driving production efficiency and in its new and additional function in the regulatory side of the industry.
“Exceeding volumes can lead to significant fines,” Brown said. “There are companies currently being fined millions of dollars for any exhaust entering the atmosphere. While the industry has typically used pneumatic actuators
powered by produced gas, every time they cycle, they release methane into the atmosphere, which leads to fines.”
While it might seem that electrification intruded into oil and gas with hardly a welcome, there is no argument that it is currently a welcomed solution to further enhance automation’s contribution. Massive retrofit projects are underway to pair electric-powered actuators with air compressors. Eliminating the need for gas-powered actuators eliminates the negative consequences associated with methane emissions.
“We have been working on a project automating compressors,” said Brown. “Historically, pneumatic diaphragm actuated valves have been used, but we have been providing electric fail-safe actuators on these types of valves, which has turned the compressor into a system with no exhaust leaving the valves.”
When compliance regulations are met, the investment in electrification can outweigh the potential expenditures associated with noncompliance fines. Money saved equals profits earned. Brown points to the savings that electrification provides. As a result, electrification is being embraced from multiple vantage points throughout the oil and gas industry.
“Downstream, plants are full of these valves—from opening and closing ball valves to opening and closing butterfly valves. along with emergency shutdown packages,” said Brown. “Anywhere you are flowing air, liquid, or gas, you can put a valve in there, and an electric actuator can control it.”
Winn-Marion has long served the oil and gas industry with automation solutions aimed at plunger and gas lift optimization, wellpad automation, and expandable pad control. Beau Warner has been with the company for 18 years and currently serves as the branch manager in Midland. He sees the oil and gas industry becoming further dependent on electrification solutions, including automation.
Winn-Marion sells and services ABB TOTALFLOW measurement and control systems to the downstream, midstream, and upstream markets. A primary solution includes a controller that operates a 60-well facility. The controller conducts shutdowns and operational procedures and measures the gas, oil, and water entering the site tanks. It also completes the handoff procedure to the midstream group.
Powering the RTU
Known as a Remote Terminal Unit, or RTU, its abilities have been used for over 30 years, but the technology continues to see improvement. Not only do they carry long life cycles—15 years, for instance—but they are offer an electrification solution, this being an
added benefit.
“This unit is powered electrically by 10 to 30 volts EC, so it is a very low-consumption solution,” said Warner. “Today, the Generation 5 Series will run at about 45 milliamps.”
Because of their unique setup, these systems also can be operated by solar and battery-supplied power. This arrangement further supports the shift to clean power solutions now available in the automation market.
Given these benefits and realized potential, electrification within automation is being considered for additional applications within the oil and gas industry. Brown indicates the future involves harnessing electrification and advancing its use. Speed, or the rate at which the valve operates, can, however, present challenges.
“You can turn massive valves with electric actuators, but they are slow,” said Brown. “If you are turning a 36-inch, 600 trim and ball valve with an electric actuator, then it’s going to have a gear operator on there for a reducing gear ratio, and then you take the place of the hand wheel with an electric actuator, so your cycle time is extended quite a bit. Big pipeline valves are required to fail closed or fail open in an emergency. Big electric actuators cannot do that.”
Electrohydraulics is not a recent technology. However, its application in responding to shortcomings in electric actuating has recently surfaced. Brown has seen how the process can create an electric actuating system.
Finding Solutions
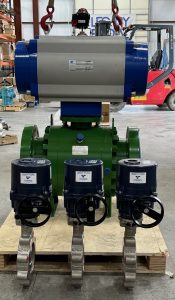
Midland-based Legacy Flow control prides itself on providing valves and automation packages for all applications.
“Essentially, you have a motor, a hydraulic reservoir, and a spring return actuator,” said Brown. “The motor kicks on and sucks the hydraulic fluid out of the reservoir and pressurizes the fluid, and it takes the place of air and compresses the spring. Those have been out for a long time.”
According to Brown, the technology has been developed, and any pneumatic actuator in the field can have the air cylinder removed and replaced with a hydraulic cylinder. Then, the hydraulic line can be tied to that hydraulic cylinder on the actuator. Through this process, a pneumatic actuator is converted into an electric actuator that is driven by hydraulics.
Brown sees an additional opportunity in automation electrification with big bore pipeline valves. Regulations require these valves to be partially stroked at specific intervals. The purpose for such regs does not have anything to do with interrupting flow. Rather, the regs are in play because there is a perceived need to get the valve off its seat and then back to its original position. Why? It’s to prove the valve functions correctly.
Automation electrification is attracting growing interest. Proponents of this technology are making a difference. By analyzing what automation electrification has already accomplished and analyzing its promises for the future, they see much to be gained. Growing numbers of proponents are calling for increased use—a trend that is paving the way for improvement.
“I think the largest push is efficiency with government oversight,” said Warner. “We are all living on this planet, and we all have to think about what tomorrow entails, but we also need to do it efficiently and effectively. I think electrification allows us to have longer uptime and less downtime while allowing the fossil fuels we are pulling out of the earth to provide the power we need. Power [generated by] power plants running on natural gas, coal, and other fossil fuels.”
Accentuating the Positive
While the upside to electrification in automation solutions looks strong, the initial conversion to utilizing these products demands an initial investment. Warner explains that while the transition might not have budgeted in [most businesses’] planning processes, the efficiency that is to be gained in the future certainly supports the need to spend money in the present in preparation and setup.
“I think the evolutionary gains are far beyond those minuscule costs we see today, whether that results in clean air—because we are not emitting methane and we have an onsite air compressor running clean air—or the simple fact that we do not have to have diesel spent generators on every location because we are using line power or capturing the energy all around us with solar and battery,” said Warner.
Companies increasingly have come to accept advancements in energy supply, an acceptance that taps the same spirit rallying the energy transition. If electrification in automation continues to offer innovative solutions for meeting emission control regulations while driving efficiency, profitability can be expected to soar. That prospect will catalyze the demand for electrified automation systems, which will assist companies like Nava Control Solutions, Legacy Flow Control, and Winn-Marion in seizing a unique opportunity while contributing to a clean energy future.
“Electrification is big business that is only going to get bigger,” said Brown.
Nick Vaccaro, owner of Vaccaro Group LLC, services the energy industry as an HSE consultant and freelance writer. A contributor to numerous industry publications, Vaccaro holds a BA in photojournalism from Loyola University. He can be contacted at 985-966-0957 or nav@vaccarogroupllc.com.