Strong words, maybe, but there’s a case to be made that proppants are the stuff that made the Permian miracle—and the world’s miracle—happen. Here’s a primer on why proppants are paramount to productive pathways.
By Julie Anderson
Adults brush it off their skin, shake it from their hair, and dump it out of their shoes. Children scoop it, mold it, and make castles out of it. Many a beach-goer has buried himself in it.
When it comes to the oil and gas industry, sand is anything but an annoyance, and it is certainly not a plaything. In fact, one expert in the field described frac sand, or proppant, as “The Greatest Oilfield Innovation of the 21st Century,” http://info.drillinginco.com/proppant-the-greatest-oilfield-innovation/.
“Without sand, or more generally proppant, there is no hydraulic fracturing, without hydraulic fracturing there is no opening of tight oil and gas plays, there is no economic advantage to horizontal drilling, there is no rise of pad drilling,” wrote Eric Roach, editor of Drillinginfo’s blog and author of the proppants post. Drillinginfo is a comprehensive information resource tool providing up-to-date land, leasing, well, and regulatory data through a search application.
In today’s world of drilling rigs and pump jacks, frac sand is known as a proppant because it literally props open the pores and cracks in rock after that rock has been fractured, enabling the oil and gas to flow to the wellbore and be pumped out.
Schlumberger defines proppants as “sized particles mixed with fracturing fluid to hold fractures open after a hydraulic fracturing treatment. In addition to naturally occurring sand grains, manmade, or specially engineered, proppants, such as resin-coated sand or high-strength ceramic materials like sintered bauxite, may also be used. Proppant materials are carefully sorted for size and sphericity to provide an efficient conduit for production of fluid from the reservoir to the wellbore.”
As explained by Roach, the first proppant was simply sand. However, over time other materials have been incorporated—by integrating these other materials into the proppant, developers have been able to vary some key properties:
Size—the physical size of the proppant needs to be adjustable per the condition of the rock. Typically measured between 8 and 140 mesh (106 µm – 2.36 mm).
Geometry—in some cases the shape of the proppant needs to be adjusted.
Weight—largely depending on the depth of the frac, the density of the proppant will need to be adjusted.
“By adjusting these properties, we can create the optimum pathways for the extraction of hydrocarbon,” Roach said. Some important measured qualities of proppant are:
Conductivity—basically the amount of flow that the proppant will allow.
Crush Resistance—deeper wells and varied lithologies require different stress properties.
Acid Solubility—tests of solubility in acid can indicate contaminants and determine how the proppant is likely to perform underground.
Proppant Qualities
Sand used as proppant must have certain qualities, including, among others, strength, sphericity, and roundness, said Don Weinheimer, vice president and general manager of oil and gas at U.S. Silica, http://www.ussilica.com. With 17 mines, U.S. Silica is one of the world’s top three proppant producers.
The American Petroleum Institute/International Organization for Standardization (API/ISO) has established standards for certain mesh sizes of proppant ranging from 12/20 to 40/70, Weinheimer said. To meet API specs, proppant must be tested against a set of industry standards. The categories of these qualifications are as follows:
API/ISO properties:
Turbidity (NTU)
Krumbein Shape Factors
Roundness
Sphericity
Bulk Density
Particle Density
Particle Size Distribution
Mean Particle Diameter
Median Particle Diameter
Solubility
Crush Resistance Classification (K Factor)
“While all properties are important, three properties are particularly critical to the success of the fracturing process,” Weinheimer detailed.
The first is turbidity, which is a measure of the cleanliness of the sand. Next is particle size distribution, which will vary from coarse grains to fine grains within a particular mesh size. The particle size distribution affects the conductivity or the ability of the proppant to create channels that allow the oil and/or gas to flow to the wellbore.
While the API sets the parameters for the particle distribution within each mesh size, each proppant company develops its own particle distribution formula within this range. Therefore, the conductivity achieved from one company’s product may, in fact probably will, vary from the conductivity of the same product produced by another company.
The third property, and “possibly the most important,” Weinheimer said, is the crush resistance classification (K Factor), which is a measure of the crush resistance of the proppant under pressure. Pressure gradients vary among reservoirs, and pressures vary among zones within the reservoir. Deeper zones require proppants with greater crush resistance.
Permian Basin Proppants
Unlike some of the other relatively newer shale plays, the Permian Basin has transportation infrastructure, as well as mid-stream infrastructure, Weinheimer said. Drilling and production are not limited by climate such as the Bakken or areas of the Marcellus and Utica in the Northeast.
Many of the reserves in the Permian Basin are relatively shallow, where excellent production rates can be obtained using quality raw sand, Weinheimer said. Shallower zones can be successfully fractured using sand from the Hickory formation in Central Texas, which is about three hours from Midland by truck. As deeper zones are fractured, operators may utilize an Ottawa or Northern white sand, which has greater crush resistance than Hickory sand.
“Although raw sand is utilized for the majority of the fracturing process, many operators seek to improve conductivity and reduce flow-back by tailing in with resin-coated sand near the wellbore,” Weinheimer said.
The most noteworthy change in completion designs is the use of significantly greater volumes of frac sand and the utilization of finer mesh sizes, Weinheimer said.
“The demand for 40/70 and 100 mesh has grown exponentially in the past two years,” Weinheimer explained. “Greater volumes of frac sand per stage combined with completion designs calling for more frac stages per well have significantly increased the demand for raw sand.”
Part of the use of finer mesh sizes is driven by the use of “slickwater fracs,” as companies move away from the use of more viscous frac fluids which can suspend the heavier particles found in a coarser mesh size, said Weinheimer.
Continued Development
When it comes to technological advancement, Brian Goldstein, product director with Fairmount Santrol, points to proppant transport technology, a hydrogel polymer wrapped around sand or ceramic proppant that resists settling in a low-viscosity fluid to uniformly distribute proppant throughout the full length of a created hydraulic fracture.
Headquartered in Chesterland, Ohio, Fairmount Santrol (NYSE: FMSA) is a provider of sand and sand-based products used by oil and gas exploration and production companies to enhance the productivity of their wells, http://fairmountsantrol.com/, http://propelssp.com/.
“Propel SSP technology ensures better proppant transport,” Goldstein said. “Each proppant grain can be transported easily to stack higher in the formation for maximized propped length and height.”
Once hydrated, Propel SSP technology reduces the specific gravity of frac sand to 1.3 from about 2.6, creating a better transport mechanism at low proppant concentrations, said Goldstein. At high proppant concentrations, the suspended proppant eliminates the duning effect of frac sand, enabling uniform proppant distribution throughout the fracture. The hydrogel coating also minimizes costly wear and tear on pumping equipment caused by uncoated sand.
Cost per BOE decreases by increasing the stimulated reservoir volume and hydraulic fracturing efficiency, Goldstein continued. Operators are efficiently placing proppant into the fracture without settling from the frac fluid; reducing and/or eliminating proppant pack and formation damage compared with crosslinked gel; and using less water, chemicals, and time to complete frac stages. Fairmount Santrol introduced Propel SSP technology in February 2014.
In 2014 and 2015, the Society of Petroleum Engineers published papers authored by employees of CARBO Ceramics Inc., which detail additional emerging technology. CARBO Ceramics Inc. is a Houston-based oilfield services technology company that provides production enhancement and environmental protection solutions, http://www.carboceramics.com/.
“New Technology Yields Ultra High-Strength Proppant” was written by Terry Palisch, Brett Wilson, and Bob Duenckel, all of CARBO Ceramics, Inc. The following is an excerpt from the abstract:
Nearly all of the proppant available on the market today can be classified into one of three tiers—sand, resin-coated sand and ceramic. The products contained in these three tiers have served the industry well and have typically covered the broad spectrum of applications required by completions engineers. However, with the development of deeper reservoirs as well as the ongoing look at geothermal and steam-flood applications, there now exists a gap in proppant technology. No conventional proppant can provide the required conductivity at the 20,000 psi closure stresses (and higher) anticipated in the Lower Tertiary formations in the deep Gulf of Mexico. Similarly, no conventional proppant can adequately withstand the harsh chemical conditions in many geothermal and steam-flood applications.
A new proppant has been developed and commercialized to meet these challenges, achieving twice the baseline conductivity of any conventional proppant at these high stresses, and providing additional advantages with increased durability and longevity. To access this paper, go to OnePetro, http://bit.ly/1AcEjlQ.
“Effective Scale Prevention Using Chemically Infused Proppant—A Uinta Basin Case History,” was authored by Joshua G. Leasure, Robert J. Duenckel and Jeff Hebert, all of CARBO Ceramics Inc.
Scale deposition down hole is a well-known and common production problem throughout the industry. Successful treatment of scale where it is first deposited near wellbore can be challenging in many cases, and sometimes impossible in others. While production assurance and scale inhibition chemicals have traditionally been added as a liquid in the fracturing fluid, this approach is often not very efficient or effective as a standalone inhibition strategy. Quite often a significant fraction of the chemical immediately returns during the initial flow back with only a small portion remaining for future inhibition. This then typically necessitates reapplication of the inhibitor chemicals using a squeeze treatment or continuous injection.
The chemical delivery system described here utilizes porous ceramic proppant, which has been infused with the appropriate production chemical(s) and encapsulated. The infused ceramic proppant is added at a designed small weight fraction to the rest of the proppant volume in the fracture treatment. It is manufactured to perform as both a proppant and a chemical delivery system so it replaces an equivalent volume of standard proppant in its dual function as a proppant [Duenckel, 2014]. After placement in the fracture the chemical slowly releases from the proppant over the designed treatment period. This chemical delivery system allows for a large amount of chemical to be placed within the fracture, releasing slowly, without negatively impacting conductivity. The proppant is encapsulated with a semipermeable membrane which controls the release of production chemicals during placement and production. This provides long-term scale protection and production assurance, which eliminates the need for additional costly well treatments and lowers overall lease operating expense. To access this paper, go to OnePetro, http://bit.ly/1IOf0HU.
Question Checklist
Whether it is a well-known “tried-and-true” proppant or a newly developed product under consideration, how does an operator go about selecting the right product?
“The quality of the proppant should be of primary importance,” Weinheimer said. It should meet API/ISO specs and be tested in an independent lab.
“Prior to the decline in oil prices, demand for proppant exceeded available supply, forcing many operators to utilize sand that has become known as “fit-for-purpose,” Weinheimer said. “Generally, this sand is substandard in that it does not meet industry specifications.”
Important questions operators should ask include:
Is the sand available in sufficient quantities to complete the job? Although the supply/demand imbalance has changed with the drop in oil prices, large volumes of finer mesh sizes may still be difficult to secure, Weinheimer said. Adequate supplies of 40/70 and 100 mesh may be more difficult to source.
Is the proppant located near the well site? In the past few years, it has become increasingly important to source proppant supply close to producing basins. A completion design for one well may call for 10,000 tons of proppant or the equivalent of 100 rail cars. Transload facilities with large storage capacity in-basin enable an oilfield service company to reduce logistics complications associated with large frac jobs that are common in today’s drilling environment.
Julie Anderson, based in Odessa, is editor of County Progress Magazine, and is well known to many readers of PBOG as the former editor of this magazine.
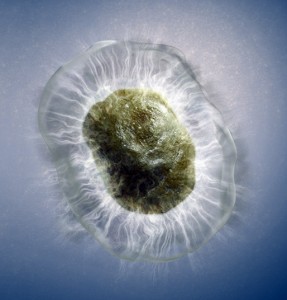
Photo courtesy of Fairmount Santrol
Propel SSP proppant transport technology, a polymer coating wrapped around a conventional proppant, rapidly swells upon contact with water. The swollen, suspended proppant travels farther and stacks higher in the formation, increasing the stimulated reservoir volume for decreased cost per BOE.