In this month’s miscellany of articles, the theme of newness might be the tie that binds. These are the full versions of the “Drilling Deeper” news items that appeared as abbreviated versions in the print edition of PBOG’s January 2018 issue.
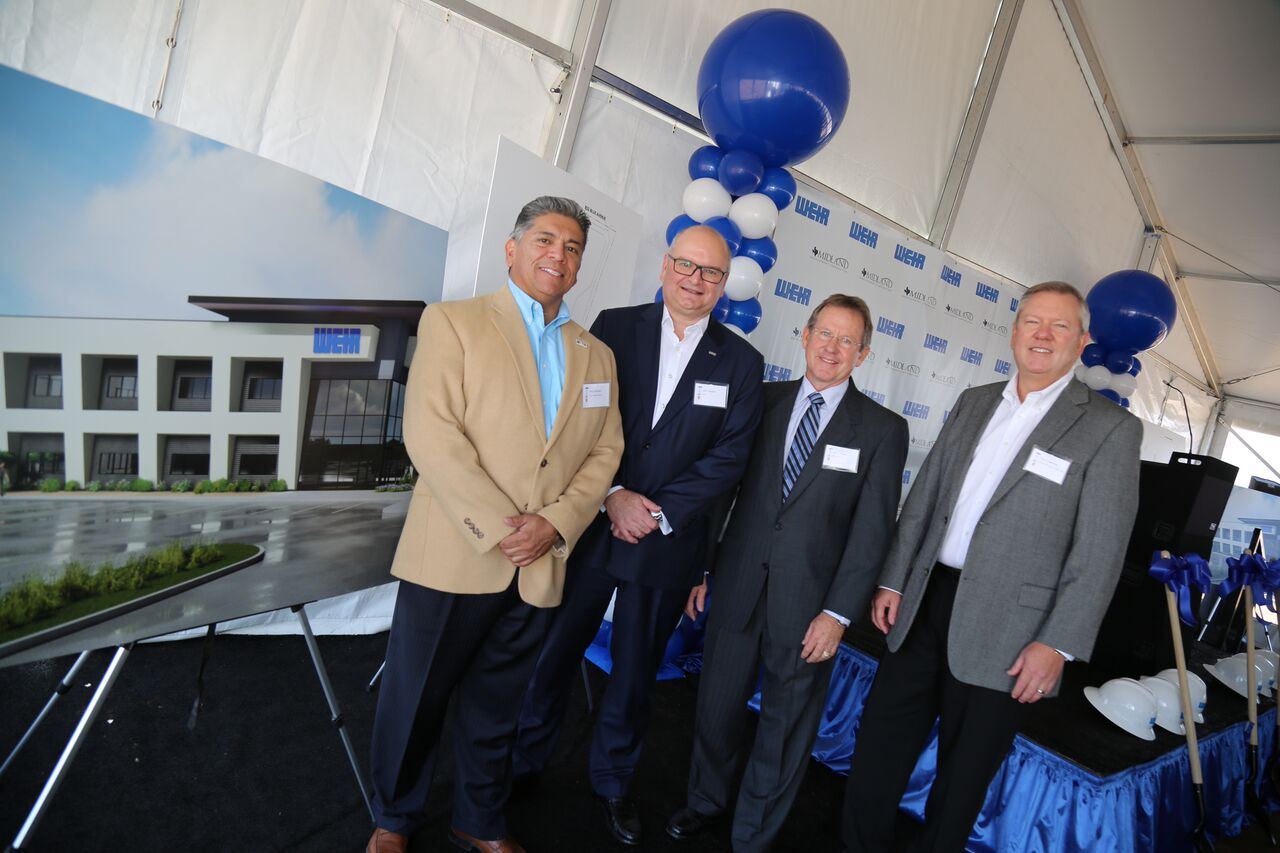
Weir Erects Service Center
Fort Worth-based Weir Oil and Gas broke ground in November on a 92,000 square-foot customer service center that will be located at the David Mims Business Park on Interstate 20 in Midland. The new center reflects the company’s strong commitment to the Permian Basin region, consolidating three existing Permian-area service center locations into one central location.
The state-of the art, purpose-built facility is scheduled to open by 2019 and will offer pressure pumping and pressure control testing facilities, a central hub for field-service operations, office space, a shop area, and a warehouse.
Attendees of the ground breaking included Jon Stanton, Chief Executive Officer of Weir Group, PLC, Paul Coppinger, President of Weir Oil & Gas, Jerry Morales, Mayor of Midland, Texas and Brent Hilliard, Midland Development Corporation Chairman.
“Our investment, as a whole, will benefit our company and employees, the Permian Basin and the city of Midland,” said Paul Coppinger, Weir Oil and Gas President. “It provides a fully integrated, one-stop shop for customers in the Permian Basin and a world-class working space for our employees. We are thankful for Midland’s Economic Development Committee in partnering with us to make this project a reality.”
The new Customer Service Center will support an estimated 100 jobs totaling a minimum of $5 million in annual payroll and bring nearly $30 million in capital and personal property investment into the county by 2019.
More information on Weir’s oil and gas operations can be found at http://www.global.weir/industries/oil-and-gas/.
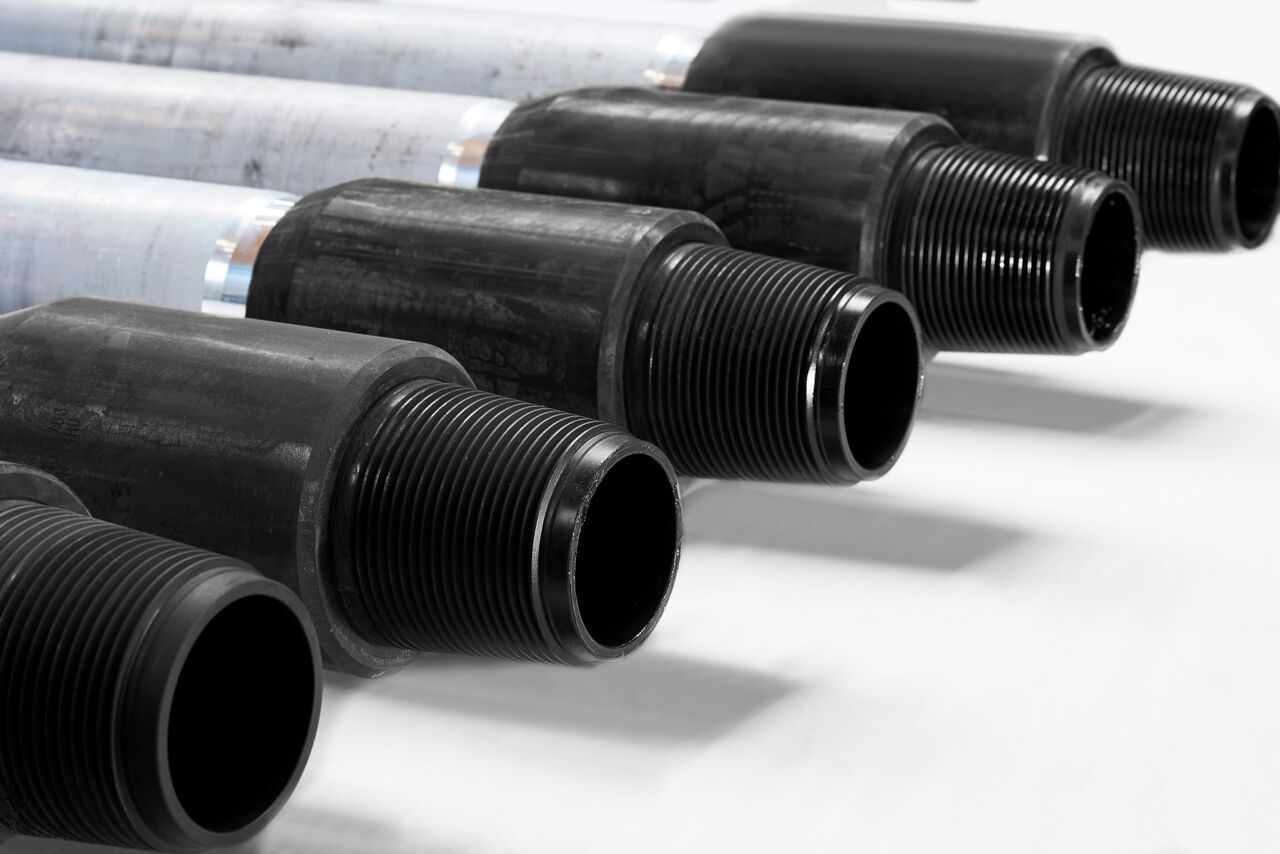
German-made Drill Pipe
The age of the aluminum drill pipe is upon us. The FuchsRohr AluDrill aluminum alloy pipe is marketed as a lightweight, efficient, and highly durable alternative to conventional steel pipes commonly used in the oil and gas industry. As drilling operations in Colorado´s Niobrara formation have shown, the aluminum alloy pipe’s material properties are able to improve drilling efficiency with up to a 30 percent ROP increase in sliding mode possible.
Peter Kaufmann, president of OTTO FUCHS Drilling Solutions (OFDS), the company which develops and produces the aluminum pipes, cited advantages for drilling operations in demanding downhole and subsea surroundings: “Our pipes are up to 50 percent lighter than similarly-sized steel pipes and completely stable. This helps our clients to save time and money. Among its many benefits, AluDrill pipe can extend the drilling depths of existing installations, which eliminates the need for cost-intensive rig upgrades.”
OFDS is part of the OTTO FUCHS Group based in Meinerzhagen, Germany. This group leverages its extensive experience in metal processing to develop innovative solutions across many key industries. Otto Fuchs established the business in 1910 as a brass foundry. Over the course of more than 100 years, the company grew into an integrated product and service solutions provider with a wide range of clients across the aerospace, automotive and construction industries. Today the OTTO FUCHS group of companies employs more than 9,000 people worldwide and generates an annual turnover of more than USD 2.5 billion.
Comprised of aluminum as well as alloying elements copper and silicon, the specially designed alloy employed in FuchsRohr AluDrill pipe had already demonstrated its lightweight and robust qualities in the demanding aerospace industry before engineers discovered its potential for oil and gas drilling operations.
OFDS is an integrated product and service solutions provider specializing in bringing high strength-to-weight ratio metallic solutions to the upstream oil and gas industry. The company offers a broad range of aluminum and titanium alloy products to the market with the goal of helping customers achieve greater reach and higher speed at less cost. For more information visit: http://www.otto-fuchs-ds.com.
Wireless, IIoT Level Up
Maybe they weren’t meaning to deliver a primer on the shortcomings—and solutions—associated with wireless instrumentation, but that’s what the makers of a wireless instrumentation system have effectively done. Along the way, they’re showing how wireless systems integrate into the Industrial Internet of Things (IIoT), and how the IIoT itself can “level up,” so to speak, as it achieves greater and greater integration and sophistication.
But we get ahead of ourselves.
First, some definition. The Industrial Internet of Things utilizes wireless instrumentation and other types of installed sensors to collect and share information with other parts of the system where machines essentially “learn” from other machines. Manufacturers, in aligning their wares with the IIoT, expect to identify inefficiencies, remove bottlenecks and streamline operations to become more competitive and profitable.
“The Industrial Internet of Things is about getting around the cost and complexity of conventional deployment,” says David Lafferty, founder of Scientific Technical Services and former Chief Technology Officer at BP, where he was involved in the early development of industrial wireless. Lafferty recommends the wireless instruments offered by longtime manufacturer Adaptive Wireless Solutions, which do not have a display, membrane switches, or external ports.
Wireless instruments provide critical information on physical processes such as temperature, pressure, level, flow, and humidity to wireless sensing networks, including WirelessHART, ISA100, Zigbee and other 802.15.4 networks.
Used to monitor the operating conditions and health of industrial equipment from engines to motors, pumps, valves, and compressors, wireless instrumentation is often used in conjunction with control systems as well as for predictive and preventative maintenance programs.
However, despite playing such a key role, these devices are often expensive, difficult, and time consuming to install. This extends both to “physical” issues such as initial set-up requirements and location of the antenna, to information security and connection with the gateway network.
In addition, ongoing support, upgrades, and device/battery replacement often equal, and even exceed, initial installation costs.
According to Lafferty, the high costs of deployment and support are the primary barriers preventing industrial wireless from “reaching its full potential.”
“If you look back to when WirelessHART was initially launched 13 years ago, we thought there would be more large scale wireless deployments by now,” says Lafferty.
A more realistic, real-world example today is, “three wireless temperature sensors at the other side of a parking lot because they didn’t want to tear it up; as opposed to ‘I have 10,000 instruments in my plant and three are wired.’ This is backwards,” says Lafferty.
Today, the drive to reduce the costs of wireless deployment is spurring a re-evaluation of the design of such devices, which has changed little in the past decade.
As a result, new options on the market now address some of the fundamental deficiencies of these devices. This includes separating the sensor from the antenna so it can be placed at a distance for ideal signal transmission; a vastly simplified user interface allowing for installation in minutes; and the inclusion of built-in, world-class security features.
Simplifying Deployment
In many cases, wireless instruments are used in hazardous environments so they need to be certified as intrinsically safe (IS) or explosion-proof (XP). Given the hazardous environment in plants, installing these instruments should be as simple and quick as possible for safety reasons, as well as to minimize time and disruption within the plant.
Unfortunately, traditional wireless instrumentation has a notoriously poor user interface that often involves tiny LCD displays and small membrane switches that are difficult to utilize in the field. The degree of difficulty increases when the devices are high up on equipment, buried deep in pipework or manipulated by installers wearing gloves.
Even the simple task of entering “join” key codes used to authenticate wireless field devices joining the network can be difficult. With traditional wireless sensors, this can involve entering 32 or 56 characters into a small handheld device with security features that obscure characters already entered.
According to Lafferty, the “ease of use” concept should not be minimized, given the fact that the industry is losing a large percentage of its installed base to retirement.
Today, younger, less experienced and often less trained personnel are simply not used to reading the instruction manual to see how products work and should be installed. As a result, even seemingly minor design features can simplify installation.
In reality, displays or small buttons are not mandatory if the wireless instrument is properly designed. Nor are dedicated ports for connecting to external communications devices that essentially substitute for the display/buttons, and cost thousands of dollars.
Lafferty points to the wireless instruments offered by longtime manufacturer Adaptive Wireless Solutions, which do not have a display, membrane switches or external ports.
Instead, all interaction occurs through a web browser on a cell phone or tablet. This is possible because the instruments work on their own Wi-Fi network, which is only utilized for tasks like configuration to conserve battery power.
For the unit itself, the application of a push on the housing (like honking the horn on a steering wheel) and LED lights used for visual confirmation of connection are all that is required to add instruments to the network. Even when replacing a unit, this task takes only about 15 seconds. With traditional models, it can take hours to days.
“When you are talking about a project to deploy 5,000 sensors, if you can shave two hours off of each sensor deployment at $85/hour per installer, it adds up very quickly,” says Lafferty.
Another installation issue involves the placement of the antenna.
With traditional wireless instruments, the sensor and antenna are typically combined in a single device that must be installed at the point of measurement. This often means the antenna is in a location with poor line-of-sight to the WSN.
For this, Adaptive Wireless Solutions redesigned its instrument to be separated into two parts: the end node (with highly accurate sensors at the read point) and the central controller, which contains the antenna.
The ability to move the central controller some distance from the end node, wirelessly, allows for better signal reception/transmission within the plant. Up to 8 end nodes can be connected to a single central controller using a Bluetooth low energy (BLE) radio link that is controlled to minimize power usage.
The central controller then communicates back to the WSN network. With this design approach, end nodes can be moved or added behind the central controller without the WSN being affected.
This stands in stark contrast with the traditional approach, where all instruments are connected directly to the WSN and so consume resources including power and address space (limited numbers of nodes per gateway, for instance).
Because most networks like WirelessHART involve a mesh architecture designed for resiliency and redundancy of communication paths, adding nodes increases the number of possible paths dramatically (square law). This can get out of control rapidly, slowing installation and creating network instability.
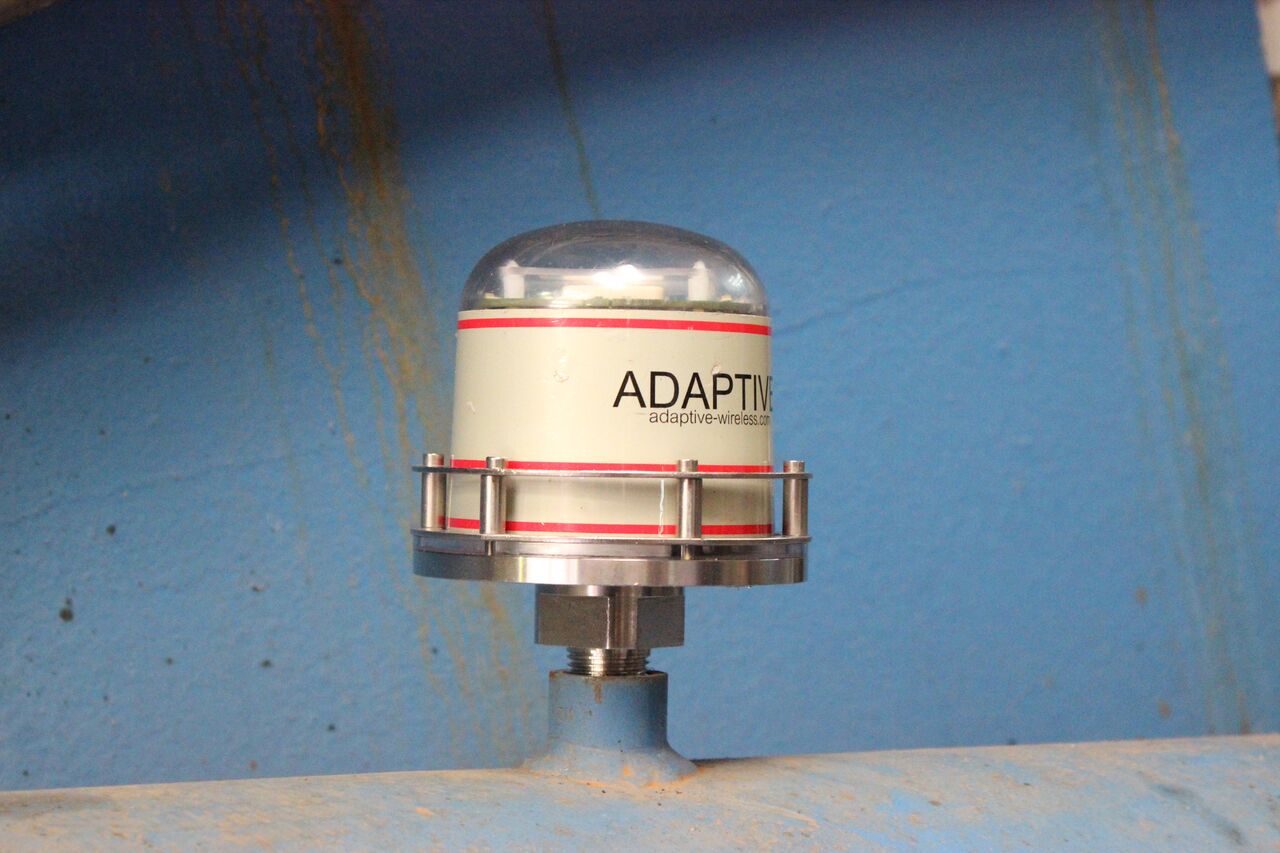
Managing Support Costs
Once the wireless instruments are installed, ongoing support, upgrades and battery placement can significantly increase overall costs.
“The ongoing costs are really coming to light as existing wireless instruments in the field are now getting to the point where it needs updating or replacing,” says Lafferty. “In many cases, it can cost the same as the initial deployment.”
Ideally, installers want to treat these devices like a light bulb: when it burns out, just replace it. However, firmware updates and current settings stored in the device are often lost when a node is removed or fails.
In a more elegant solution, Adaptive Wireless can clone the configuration of any member of the central controller group, even after the node is removed or even destroyed.
To accomplish this, configuration information is stored in all other nodes, redundantly, and so can be reconstituted or cloned by simply transferring the data. So long as one device within the cluster is intact the others can be quickly and easily reconstructed in the field.
“Adaptive Wireless has the ability to clone the entire configuration of the device so that the new instrument is an exact clone,” explains Lafferty.
Wireless updates and frugal use of power have been so carefully designed, and to such a degree, that batteries don’t need replacing – the unit grows old before the battery dies – further reducing the cost and complexity of replacing devices.
“With the cost of ongoing maintenance dramatically reduced, [wireless instrumentation] is now a solution that can be scaled up to the kinds of numbers needed for the digitalization effort happening in many industries,” adds Lafferty.
This includes the Industrial Internet of Things (IIoT), for which Lafferty is currently doing business development and consulting through his company Scientific Technical Services.
For more information, contact Adaptive Wireless Solutions at (978) 875-6000; write 577 Main Street, Hudson, MA 01749; or visit www.adaptive-wireless.com.