Technology on Parade
On April 12, in Midland, Weatherford International welcomed customers, employees, and students as well to see and hear about cutting-edge technologies that the services firm is employing in the Permian Basin. The Petroleum Museum was the venue for the two-day event. Weatherford CEO Mark A. McCollum was on hand, as well as other key staffers, to answer questions and carry out the mission of the company’s Worldwide Initiative Supporting Education, also know as Weatherford WISE. On Friday morning (the 13th), Weatherford hosted students from Midland College and the University of Texas Permian Basin.
Some of the technologies featured at the event included the Minima composite frac plug and the Rotaflex long-stroke pumping unit. Weatherford’s stated purpose for its event was to help attendees “discover how [Weatherford’s] resource expertise, innovative technologies, and local talent help maximize a company’s return on investment in the Permian Basin.”
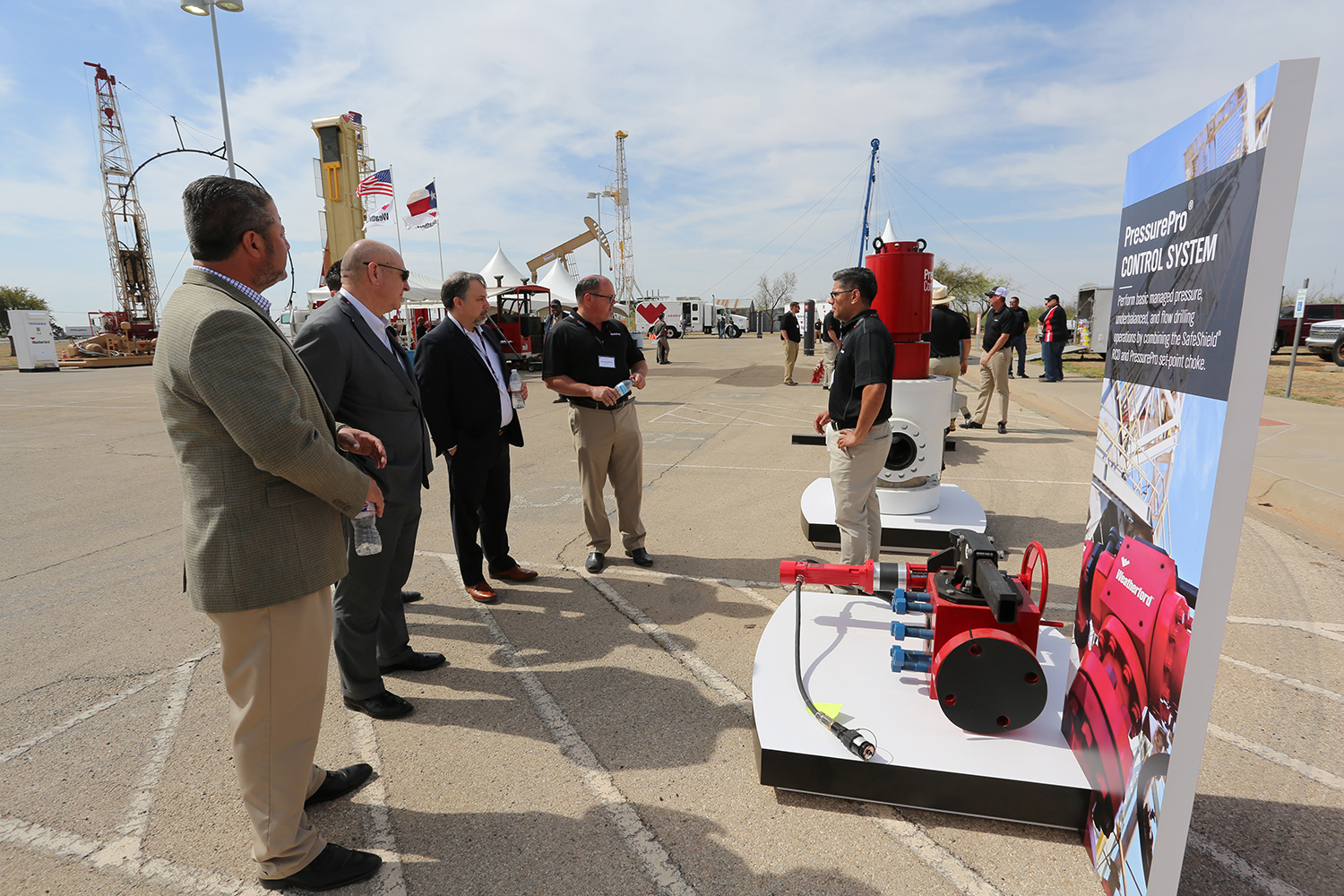
The outdoor portion of the Weatherford WISE event included exhibits of the company’s state-of-the-art hardware. Mark A. McCollum, CEO of Weatherford, stands second from left.
Jet Pumps: Worth $3 Mill
Pertamina, the national oil company of Indonesia, recently awarded a $3 million contract with Production Lift Companies, for their hydraulic jet pump systems. Systems include re-engineered downhole jet pumps and bottomhole assemblies as well as new technology process systems. The equipment is for mature wells in low pressure gassy oilfields (Indonesia’s Bunyu and Sembakung fields, in this instance) that require low maintenance, reliable systems that must take into account life-cycle economics. The fields are located in Kalimantan, Indonesia, where producing formations consist of interbedded sand and shale at subsea depths of 2,400 feet to 3,400 feet, with permeability of 180-900 md, porosity of 20 percent to 30 percent and water saturates estimated at 30 percent to 40 percent and GOR between 150 scf/bbl to 4000 scf/bbl. Initial reservoir pressure in the 80’s was 1214 psi, but current estimates are slightly above 600 psi. Production Lift Company’s Technical Engineer, Jesse Hernandez, headed the design and applications engineering. Production Lift Companies is located in Midland, Texas, and has been serving the Permian Basin for 30 years.
Sand Gets More Affordable
A major report from Energent, part of Westwood Global Energy Group (Westwood), the energy market research consultancy, predicts dramatic changes to the frac sand supply chain to the Permian Basin—the world’s most important oil growth region. The Permian Basin produces 2.9 million barrels of oil per day, approximately 45 percent of light-tight oil production in the United States. More than 800 E&P operators, 25 pressure pumpers, and 30 frac sand producers are engaged in activities there. With 2,430 drilled uncompleted wells and increasing capital expenditures for E&Ps in the Basin, the Permian is poised to continue growing. Mines based within the Basin itself are now producing sand of the required technical standard and volume to meet the expected demand growth of 2.5 million tons per quarter over 2018-19. By the end of 2018, Energent anticipates over seven million tons per quarter of available premium sand capacity inside the Permian Basin. This will remove almost 800,000 tons of sand requiring long-haul rail logistics in 4Q18 compared with 1Q18. The report “Frac Sand in the Permian: Near Term Outlook,” is available for purchase at energentgroup.com.
Frac sand, a raw material that is vital to the industry, is pumped into the ground at high pressure to help extract oil and gas. Until now, the industry has relied upon Northern White premium frac sand, hauled over 1,200 miles from Wisconsin at a cost of $110 per ton.
The Energent report shows that all this is about to change. Mines based within the Permian basin itself are now producing sand of the required technical standard and volume to meet the expected demand growth of 2.5 million tons per quarter over 2018-19.
By the end of 2018, Energent anticipates over seven million tons per quarter of available premium sand capacity inside the Permian Basin. This will remove almost 800,000 tons of sand requiring long-haul rail logistics in 4Q18 compared with 1Q18.
Todd Bush, Founder of Energent, comments: “The cost and availability of frac sand has been a major challenge for operators in the region. So much so, that new entrants and existing frac sand companies have dedicated over $850 million to opening their own miles near Winkler County, Texas.
“The potential savings of in-basin sand are huge – as long as operators are satisfied that it meets their technical requirements, they could save up to 50 percent on frac sand hauled from Wisconsin.
“Assuming a 50 percent adoption rate of locally mined sand, incumbent suppliers will see a material decline in non-contracted volumes by the third quarter. It will also focus attention on logistics within the basin itself – the truck fleet, retaining drivers and transport technology – which will also drive well economics.”
The full report—Frac Sand in the Permian – Near-Term Outlook—has been put together using Energent and Westwood’s proprietary data detailing frac sand demand and consumption patterns across the US shale plays. For a direct link to the report, go to: http://energentgroup.com/in-basin-frac-sand-supply-demand-report/.
Agencies Urge Repeal of Clean Power Plan
The Railroad Commission of Texas has joined the Texas Commission on Environmental Quality and the Public Utility Commission of Texas in submitting comments on a U.S. Environmental Protection Agency proposal to repeal the Clean Power Plan. A letter signed by the executive directors of the RRC, TCEQ and PUCT was submitted to EPA April 26 by TCEQ. The letter includes comments on EPA’s proposed repeal of Carbon Pollution Emission Guidelines for Existing Electric Utility Generating Units, otherwise known as the Clean Power Plan. “The PUCT, RRC, and TCEQ support the repeal of the Clean Power Plan,” the letter states.
Company Supports Charities
ConocoPhillips recently announced the presentation of $200,000 in charitable grants to 35 organizations in the Permian Basin. “These organizations serve some of this community’s most critical needs, and we are proud to support their efforts,” said Johnny Golden, manager, Mid-Continent Operations, ConocoPhillips. This year’s recipients include volunteer fire departments, educational institutions, United Way, and Boys and Girls Club chapters throughout Andrews, Ector, Eddy, Lea, Midland, and Wink counties. Each year, ConocoPhillips invests in local communities through charitable giving, employee volunteerism, and sponsorships. The donations support education, health and safety, natural resources, the arts, civic and social services and disaster relief.
Kermit Gets New Facility
Variable Bore Rams, Inc., one of the largest original equipment manufacturer (OEM) ram and blowout preventer (BOP) component providers in the world, has opened a new facility in Kermit, Texas. VBR provides a wide variety of BOP rams manufactured by Cameron, GE (Hydril), and NOV (Shaffer). With access to the 9,000 sq. ft facility, which spans 5 acres of land, VBR has extended its reach further into West Texas and surrounding areas. President of VBR, Hines M. “Chip” Marshall, Jr., said, “We have a complete line of variable bore, fixed bore, dual, casing and shear rams ready to ship worldwide at a moment’s notice. Our new Kermit facility will handle both shipping and receiving of ram rentals, enabling faster equipment delivery and easing access logistics for our customers in West Texas, New Mexico, Oklahoma, and Colorado.”
Variable Bore Rams Inc. provides support for blowout prevention operators worldwide and offers a wide variety of BOP components and products, including rams and elastomers. Stocking the latest in equipment and providing the most recent product upgrades, engineering updates and technical bulletins, VBR provides services worldwide, 24 hours a day, seven days a week and at a moment’s notice. For more information, visit www.vbri.com.
Waste Strategies are No Waste
By P. Rodger Keller, Scott Energy Technologies LLC
Shareholders and lenders are increasingly requiring oil and gas companies to incorporate sustainable practices into their core business. Investors and lenders are taking note. Companies that embrace financially, environmentally, and socially sustainable waste management practices tend to outperform their peers. With this in mind, oil and gas companies can strengthen their bottom line, reduce their environmental footprint, and enhance their social license to operate (SLO) by employing sustainable drilling waste management strategies. Drilling waste is a high-volume waste stream, with hundreds of millions of barrels produced each year in the onshore U.S. market alone. Drill cuttings and its associated fluids are conventionally viewed as a financial liability requiring disposal. Consequently, drilling waste management is traditionally approached by getting the waste “out of sight and out of mind” through practices that include landfilling, landfarming, and onsite burial. However, each of these methods has sustainability issues and risks that can adversely impact a company’s bottom line.
Landfilling and landfarming consume large areas of land and their residual impacts include leaching, runoff, air emissions, vegetation damage, toxicity to animals and uptake by humans. Social impacts of disposal facilities may consist of increased truck traffic, decreased property values, odors, noise, unsightliness and increased demands on community health services.
During the recent oil and gas downturn, numerous drilling waste management companies went into bankruptcy and left behind waste processing and disposal sites that taxpayers and waste generators (oil and gas operators) are left to clean up. This can result in a polluted parcel of land unsuitable for redevelopment for a viable tax-generating use until properly remediated.
Conventional drilling waste management practices create liability with material implications on an oil and gas company’s bottom line. If waste is not effectively contained or sequestered, contaminants can migrate and impact land, water, vegetation, wildlife, cattle, and humans, leaving oil and gas companies on the hook for remediation. When waste from various generators is commingled at a facility, each generator has essentially assumed the liability of all the waste generators for that facility. When a disposal facility operator goes bankrupt and abandons a facility, the waste generators are on the hook for remediation and closure of the site. Drilling waste remains a liability for the oil and gas company, even after disposal.
Waste management costs and environmental liabilities are not the only factors with material implications. Social license issues are inevitably tied to poor waste management practices, which can increase expenditures and negatively affect shareholder value. Social issues are often triggered by environmental issues, leading to material repercussions for an oil and gas company. Permitting delays mean lost revenue, delayed point-of-first sale (POFS) time and lost opportunity costs. Lawsuits result in costly legal fees. Negative publicity, a high-profile company-community conflict and other social factors can impact shareholder confidence, resulting in lower stock prices.
Sustainable drilling waste management strategies mitigate environmental, social and financial issues that arise from conventional waste management practices. The keys to success are source reduction and an assessment of how waste can be converted into a value-added asset, rather than a liability. An example of source reduction includes maximizing the efficiency of the mud system, which results in reduced waste volumes while lowering waste management costs. Using sound science and proven technologies to recycle drill cuttings into engineered drilling pads, production pads and lease roads perfectly exemplifies the value of turning waste into an asset.
Committing to sustainable practices will quickly pay environmental, social and financial dividends to oil and gas operators, as well as the community. Waste constituents are immobilized, protecting the soil, water, air, vegetation, wildlife and human health. Truck traffic will be reduced, a lower volume of waste will be generated and better compliance with regulatory agencies will all translate into social benefits and more positive publicity. Financial benefits include reduced costs of disposal, trucking, construction and maintenance, as well as reduced liability. Best practices can also lead to a reduction of non-productive time (NPT), which can result from poorly constructed roads and pads.
Sustainable waste management practices are not only environmentally advantageous, but also socially and financially beneficial. By recycling drilling waste in a responsible and strategic manner, oil and gas companies have a tremendous opportunity to improve shareholder value, while enhancing their community reputation.
Bio Solutions Win Recognition
An Ohio-based R&D company is developing new and innovative approaches to common industry challenges—with solutions that are gaining international attention. Scientists at Locus Bio-Energy Solutions, LLC, have created a series of unique microbial-based products that substantially increase oil reserves and reduce LOE. The products, both cost-effective and non-toxic, are evolving oil well operators’ approaches to maintenance–leading Darcy Partners to name Locus Bio-Energy a Top 10 Emerging Tech Company in the World in the production chemicals space. For years, the oil industry has been plagued with many common challenges—from paraffin, asphaltenes, biofilms, poor wettability and viscosity build up—all resulting in the gradual loss of oil recovery. Current solutions typically include hazardous, toxic chemicals which are expensive and have not produced lasting results. The patent-pending microbial blends discovered by Locus Bio-Energy have proven to be a safer alternative, from an HSE perspective for operators, and improve overall well health and protect wellbore equipment—with longer lasting, better results.
This approach, specifically in paraffin dispersal, and the resulting profit increases caught the attention of Darcy Partners, leading to global recognition as an emerging technology company. Experts from Locus Bio-Energy were invited to speak about the technology at multiple closed forums in Texas attended by many industry leaders—with overwhelmingly positive reactions.
“Microbials have been tried in the past, but never with the proper approach to confirm efficacy and survivability,” said Gary West, senior vice president of business development at Locus Bio-Energy. “Our products are fermented locally resulting in up to 1000x the potency at injection, and have been shown consistently in field trials to have a strong impact on production and recoverable reserves—meaning these treatments pay for themselves. The approach does not cause corrosive bio-films and actually dissolves them, while reducing Sulfate Reducing Bacteria (SRB) colonies—creating safer solutions that are redefining the approach to oil well maintenance.”
Locus Bio-Energy currently offers two 100 percent environmentally-safe product lines, with treatments customized specifically to the conditions of the wells being treated—AssurEOR FLOW, a paraffin dispersal product with the added benefit of an “EOR effect,” and AssurEOR STIM, a highly potent enhanced recovery application designed to stimulate reservoirs. Field trials from hundreds of well applications show increased recoverable reserves and a more than 50 percent average increase in oil sales with AssurEOR FLOW, and up to 500 percent increase in production over extended periods with AssurEOR STIM. The results are gaining attention and momentum across the industry, with new wells being treated daily.
For more information on Locus Bio-Energy and the new trend of using microbial-based solutions for upstream oil applications, visit LocusBioEnergy.com.
IFS Cites Three Key Initiatives
While oil and gas companies experienced tough years recently as oil prices plummeted to record-low levels, the recovery of the industry started in 2017, and now is the time to kick it into a higher gear to reap the benefits of being an early adopter of new technologies and business models, according to IFS. Magne Halvorsen, Global Industry Director for Oil and Gas at IFS, predicts new charging models, digital investments, and compliance solutions will be the three key initiatives that companies within the sector will be pioneering to leverage the industry turn-around in 2018.
The good news is that the cost cutting and downsizing over the past few years is now at an end, both for the oil companies themselves and their suppliers. Global demand for oil is growing in the West and in China, with OPEC recently claiming that the country will increase its forecast by 1.35 million barrels per day (b/d) to reach 98.12m b/d. With the macro-figures telling us this increase may last for the next few decades, industry players are ramping up their activity, with many playing catch-up in the digital space.
When talking to customers and prospects in the industry, I hear the need to tap into digital technologies – including cloud, IoT, big data, advanced planning and scheduling, and automation – is key to become smarter and more efficient at extracting oil and gas. Part of this is being driven by the downsizing that has taken place over recent years – with fewer crews to man rigs and facilities, organizations need to maximize the human resources to hand. Thus, automating manual tasks becomes important.
Songa Offshore is one of those at the vanguard of this push. The company has connected IoT sensors to 600 assets on each of four oil rigs throughout the North Atlantic Basin. The IoT data is fed into the ERP system which forms the basis for reducing maintenance costs and increasing productivity by driving operational efficiencies. The main potential optimization lies in the automation of work orders – if specific data points can trigger automated work orders, this will save significant time and costs.
Other potential investments are rolling in, including beacon technology to improve safety by alerting crew members when they’re in a restricted zone. Elsewhere, advanced visualization and planning tools could help oil & gas contractors speed up the drilling license application process and maximize productivity by being able to better indicate which areas they are already cleared to drill in.
With governments around the world increasingly focused on restricting pollution, 2018 will see a continued rise in demand for ways to minimize CO2 and NOx emissions as well as to accurately document them for compliance purposes. Thus, we are likely to see a move away from diesel-powered plants to the use of alternative energy sources, such as tidal, to reduce emissions. With each rig producing as much CO2 annually as 5,000 cars, there is a heavy price to pay – financially and environmentally.
Advanced compliance and risk solutions will become an essential requirement to automate the monitoring and reporting of emissions, replacing inefficient manual processes. While remote facilities have historically been difficult to connect to the internet, satellite communications are enabling a new wave of cloud-powered systems to support these efforts.
Another key evolution in the industry driving the push to become faster and more efficient at extraction involves a change in the way oil & gas companies pay their suppliers and contractors. The traditional “day rate”—the flat-fee rate a contractor is paid per day for operating, say, a drilling rig – is increasingly moving to a performance-based system.
Where an oil company might have agreed a contract of $300,000 per day for 100 days, they may offer more or even a bonus if that can be completed in 80 days. This creates new opportunities for those industry suppliers who can become more efficient. The IoT and big data analytics are key enablers here, with sensors able to feed back on various environmental and drilling conditions to maximize productivity. However, technology alone will not produce the desired goals unless organizations can break down traditional siloes between teams which monitor equipment, analyze weather conditions and those focused on other parts of the operation.
These trends can also be seen in terms of the gradual servitization of the industry. In fact, IFS research on the benefits of servitization for oil & gas companies has revealed that those looking to add innovative service and asset management capabilities to their offerings can reduce CO2 emissions by 10–15 percent and maintenance costs by 25–30 percent. One key area to do the latter is in the classification process. Every five years, floating rigs must be taken out of operation while essential maintenance checks and documentation take place. But with firms earning $300 to 400K per day, the three weeks this can take could lead to losses in the millions.
Advanced planning and scheduling technologies will therefore become a game-changer for both oil and gas companies and service providers, helping them better plan and document maintenance offshore without the need to take vessels to the yard as frequently. These are highly sophisticated systems, maximizing the human resources on board and incorporating key risk assessments of equipment to ensure any maintenance work is done and recorded according to a strict timetable.
So, what do oil and gas companies need to do to make the most of these opportunities in 2018? Fundamentally, I’d suggest that many organizations are in need of a “digital cleanse”. Many legacy tools, technologies and, most importantly, processes remain in operation that might be a barrier to innovation. Automation will not work if you are simply automating inefficient and error-prone manual processes. In fact, our recent research found that only 7 percent of global firms are successfully harnessing data-driven insight to deliver faster time-to-innovation and competitive advantage—by far the lowest of any industry studied.
Fortunately, the industry is in good shape to recover from recent years of underinvestment. Enterprises know what’s required to capitalize on the current upturn to become modern, competitive organizations. But to achieve this next level of growth, increase margins and support exciting new business models, these firms will need to invest in new digital skills as well as technologies.
Confronting Corrosion Under Insulation
Corrosion Under Insulation (CUI) is the root cause of many of the global petrochemical industry’s most serious problems including forced shutdowns, lost production, early repair and replacement, as well as safety and environmental consequences that can cost millions of dollars per incident. CUI, which involves the corrosion of vessels or piping beneath insulation due to water penetration, is insidious because it can remain undetected until the insulation is removed for inspection or leaks occur. Water penetration can result from many causes including monsoons, rain, flooding, wash downs, and sprinkler systems, as well as exposure to steam, humidity, or frequent condensation and evaporation of atmospheric moisture.
From upstream wells, risers, drilling rigs, or offshore platforms, to midstream pipelines, storage, and liquefied natural gas (LNG) terminals, to downstream refineries, fighting CUI and major corrosion has been an uphill battle and a major cost in the operation of oil and gas facilities, according to NACE International’s “International Measures of Prevention, Application and Economics of Corrosion Technology (IMPACT)” study.
Fortunately, even when traditional coatings have allowed CUI and corrosion to occur, a new approach can stop the corrosion to dramatically extend facility and equipment life in oil and gas industry applications.
Traditional corrosion protection typically involves applying polymer paints and rubber type coatings. Such methods create a physical barrier to keep corrosion promoters such as water and oxygen away from steel substrates. However, this only works until the paint is scratched, chipped, or breached and corrosion promoters enter the gap between the substrate and coating. Then the coating can act like a greenhouse – trapping water, oxygen and other corrosion promoters – which allows the corrosion to spread.
Some of the world’s largest petrochemical companies, including China Petroleum & Chemical Corporation, however, are finding success with a new approach toward stopping CUI and corrosion.
China Petroleum and Chemical Corporation, commonly known as Sinopec Corp., is one of the largest integrated energy and chemical companies in the world, with upstream, midstream and downstream operations. In Sinopec’s Jianghan Oilfield projects, located in China’s Jianghan Plain in Hubei province, there are numerous facilities for oil and gas extraction, transport, and storage.
However, with Hubei’s sub-tropical monsoon climate, CUI and corrosion are serious issues that shorten equipment life and require excessive maintenance. In this environment, traditional coatings have been ineffective, and stopping corrosion that is already underway is often the last resort.
To extend production and the service life of assets already experiencing serious CUI or major corrosion, on two sample projects Sinopec turned to EonCoat, a spray applied inorganic coating from the Raleigh, North Carolina-based company of the same name. EonCoat represents a new category of tough, Chemically Bonded Phosphate Ceramics (CBPCs) that can stop the corrosion, ease application, and reduce production downtime even in very wet, humid, monsoon prone conditions.
In contrast to traditional polymer coatings that sit on top of the substrate, the corrosion resistant CBPC coating bonds through a chemical reaction with the substrate, and slight surface oxidation actually improves the reaction. The surface of steel is passivated as an alloy layer is formed. This makes it impossible for corrosion promoters like oxygen and humidity to get behind the coating the way they can with ordinary paints.
Although traditional polymer coatings mechanically bond to substrates that have been extensively prepared, if gouged, moisture and oxygen will migrate under the coating’s film from all sides of the gouge.
By contrast, the same damage to the ceramic coated substrate will not spread corrosion because the carbon steel’s surface has been chemically transformed into an alloy of stable oxides. Once the steel’s surface is stable (the way noble metals like gold and silver are stable) it will no longer react with the environment and therefore cannot corrode.
Visible in scanning electron microscope photography, EonCoat does not leave a gap between the steel and the coating because the bond is chemical rather than mechanical. Since there is no gap, even if moisture was to get through to the steel due to a gouge, there is nowhere for the moisture to travel. This effectively stops atmospheric corrosion and CUI on carbon steel assets.
The corrosion barrier is covered by a ceramic layer that further resists corrosion, water, fire, abrasion, impact, chemicals, and temperatures up to 400 °F. Beyond this, the ceramic serves a unique role that helps to end the costly maintenance cycle of replacing typical barrier type coatings every few years.
“CUI is the silent killer,” explains Merrick Alpert,” President of EonCoat. “The insulation creates a terrarium on the steel in which corrosion is guaranteed to occur if traditional coatings are used. And the insulation then hides the corrosion from being detected until it’s too late.”
Sinopec’s first sample project using the CBPC coating involved addressing CUI on a 500 cubic meter petroleum storage tank in an oil-extraction facility in the Jianghan Oilfield.
While the storage tank’s original coatings were wrapped beneath a mineral wool insulating layer, due to rain, condensation, and moisture invasion through the damaged insulating layer, these coatings had failed, allowing CUI in a number of areas.
After peeling off the insulating layer, the metal surface underneath was prepared by sandblasting, then the CBPC coating was applied. The application has effectively stopped the CUI issue and is expected to extend the storage tank’s functional life for years to come.
After the success of the first project, Sinopec opted to utilize the CBPC coating to address serious corrosion on a container-type water injection pumping station in another Jianghan Oilfield facility. Because of the pumping station’s outdoor location with very high saline alkali content soil, along with a very humid container environment, shutdown for corrosion maintenance was typically required every three years.
A traditional three coat system was routinely used to maintain corrosion protection for the pumping station, so coating application took at least three days to allow drying time for each layer. Including surface preparation, total required maintenance downtime was at least seven days, which hindered production.
One of the greatest benefits of the CBPC coating, however, is the quick return to service that minimizes facility downtime. The time saved on an anti-corrosion coating project with the ceramic coating comes both from simplified surface preparation and expedited curing time.
With a typical corrosion coating, near white metal blast cleaning (NACE 2 / SSPC-SP 10) is required to prepare the surface. But with the ceramic coating, only a NACE 3 / SSPC-SP 6 commercial blast is typically necessary.
With traditional coatings, extensive surface preparation is required and done a little at a time to avoid surface oxidation, commonly known as ‘flash rust’, which then requires re-blasting. But with the CBPC coating, the flash rust is actually desirable. There is no need to ‘hold the blast’. The reason for this unique CBPC characteristic is due to the presence of iron in the rust, which helps to create the magnesium iron phosphate alloy layer. It is this alloy layer that allows CBPCs to so effectively protect carbon steel from corrosion.
In contrast, a corrosion resistant coating for carbon steel utilizing the ceramic coating in a single coat requires almost no curing time. Return to service can be achieved in as little as one hour, which can potentially save hundreds of thousands of dollars per day in reduced oil and gas facility downtime.
Because of these unique properties, total coating application including surface preparation of the Sinopec pumping station will take two days and the asset can be put into service immediately.
With CUI and corrosion a perennial problem for oil and gas facilities with massive carbon steel structures, utilizing CBPC coatings that can control corrosion for decades and reduce downtime will only help the bottom line.
For more information, call 754-222-4919; visit www.eoncoat.com; or write to EonCoat, LLC at 551 Pylon Drive, Unit D, Raleigh, NC 27606.