Fracking uses highly pressurized water, mud and sand to fracture shale until it releases the oil or gas trapped within its layers. Ensuring a continuous supply of the millions of gallons of water needed for this operation is a logistical challenge that is vital to wellsite cost control and profitability. Meeting this challenge has been a labor-intensive and sometimes risky process, but an IIoT automation project now underway in the Permian Basin demonstrates what may herald a new era of water management productivity and cost-efficiency.
Gallons and gallons of water
The U.S. Geological Survey estimates that fracking a single well can require up to 42 million gallons of water, depending on the length of the well bore, number of stages involved, and the proppant design. Transporting water to the site must be planned and accounted for during the initial construction phase of the well.
Setting up the projected water supply typically takes between two and eight weeks. It involves scouting water sources, negotiating rights-of-way with landowners, installing temporary or permanent piping, storing it in large membrane-lined containment ponds or tanks, and pumping the water to the wellsite. Most of the larger petroleum exploration and production companies have full-time water transition teams to handle this, but the smaller and medium-sized operators more often subcontract to water transfer service providers.
“Having sufficient water available and delivering it reliably to the frac location is a critical piece of the supply chain in completing a new well” said Reed Taylor, founder and CEO of FLOWPOINT Water Solutions, a Midland, Texas-based water transfer firm serving the Permian Basin.
Petroleum producers usually contract with FLOWPOINT to identify sources and provide the logistics needed to get water to the fracking site. Sometimes, however, the petroleum company already has a water source and they just hire FLOWPOINT to handle the transfer logistics.
Miles and miles of piping
For FLOWPOINT, the distance between the water supply storage facilities and wellsite is usually 3 to 10 miles, across which they typically lay temporary piping or lay-flat hose 12 inches in diameter. Keeping the water moving through that channel requires synchronizing operation of multiple pumps along the way, many of which may be deployed in remote points, often accessible by dirt roads only. For most of today’s transfer services, operating these pumps involves deploying field operators to travel to the various pumping sites, start or stop them as required, spot and fix leaks, and keep accurate records of transfer volume.
Thinking that there must be a more efficient way to streamline water transfer operations, Taylor began researching automation solutions but most of what he found was less effective “off the shelf” solutions that lacked scalability — until he met Harry Browne, CEO of Flow-Sync, a Texas-based automation supplier that provides specialty skid-based water transfer pump control solutions for water fracking applications that optimize and simplify complex water transfer logistics.
“Water supply logistics is a corner of the energy industry that doesn’t get much attention. While many oilfield facilities implement automation, PID loops, alarm notifications and other basic control functions, this hadn’t yet transitioned to temporary water transfer operations,” said Browne.
“On the surface, water transfer appears to be a relatively simple operation, but it presents many challenges. Getting the water to the well often involves synchronized operation of two to four large diesel pumps spread out over the entire length of the transfer line. The pumps must be started and brought up to operating speed in series and then ramped down in series to a stop every few hours. The process is repeated around the clock with each stage of the fracking operation, which can run for several weeks.
“Starting up a line may require multiple boosters, which must be sequenced manually, in stages. It can be tedious. You may turn on your first pump and experience some lag time, during which the system builds pressure, which brings you the first booster pump. If you run it too fast you could suck the line down to where it will collapse,” Browne said, adding that coordinating the process traditionally requires multiple operators, who may be communicating with each other by cell phones only and from areas where service may be spotty.
Browne has automated these processes through a combination of software applications that calculate flow rates, a cyber secure automation platform, cloud-based data storage and analytics and a SCADA interface through which operators interact with the system from anywhere using an internet connection.
Calculating the flow
An efficient operation begins with analyzing the transfer line hydraulics to determine the number of pumps required to satisfy the design flowrate and route topography. Flow Sync’s Transfer Calc software provides a simple, intuitive user interface to quickly model the entire flow operation. At job startup, the results are reconciled with readings from pressure sensors, level sensors, and flowmeters to identify equipment problems that could lead to downtime. These readings go to the control system which uses this data to optimize the flow to the site.
Controlling the flow
The complex pump control necessary to implement the flow models is provided by a PLC that Flow-Sync gets from a Bedrock Open Secure Automation (OSA) Remote industrial control system. The OSA Remote system enables automation that leverages the economies of open technologies by eliminating vulnerability to cyberattacks in a rugged package built for the extreme conditions typical of these applications.
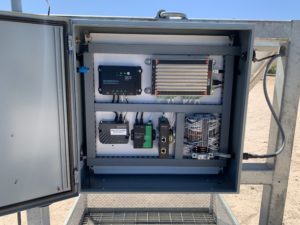
Figure 3 – The Bedrock OSA controller, upper right, provides rugged, cyber secure control that synchronizes pump operation.
Flow Sync deploys the OSA Remote control modules in the wiring cabinet of its patented, self-contained, portable skids. They are easily connected to the pumps so that the entire transfer operation can be effectively monitored and controlled from any location. The OSA Remote with universal IO is configured to read and write tags from the skid’s sensors and its OPC UA capability makes it very efficient to communicate this data to the broader system.
“I like the simplicity of having as few components as possible and being able to mount them securely,” said Browne. This simplifies assembly of new skids, improves reliability for portable equipment, and requires fewer spare parts. The Bedrock system was easy to configure. Its IDE software tool is free and very easy to use. We could not have executed the complicated pump sequencing as easily or economically with any other IDE.
“We especially liked the fact that the cyber security is built-in. Any interruptions to the data communications within our automation system could be catastrophic. If a hacker were able to gain control of the water flow, they could shut down the transfer or the fracking itself. That’s one reason we’ve chosen the Bedrock OSA Remote over other options,” said Browne, adding that robustness was another reason.
“We are deploying these devices in the desert, so the fact that Bedrock is temperature-rated up to 176°F (80°C) is important to us,” he says. Plus, we are transporting all controls on a trailer, over some pretty rough roads, and it takes a beating. The first control platform that I used was a custom-designed board using an inexpensive PLC and we had vibration issues. We have not seen any of these problems with the Bedrock system,” he says.
Interacting with the system
Enabling users to interact with the automation system is Ignition SCADA software from Inductive Automation. The Ignition server integrates with the Bedrock controls and the AWS cloud, where Amazon Elastic Compute Cloud EC2 servers host an SQL database. This IIoT architecture is fully scalable in terms of processor memory and disk storage. The OPC UA connection with the Bedrock OSA Remote extends the secure PLC architecture to remote locations via TCP/IP.
The big picture
The combination of the Bedrock OSA Remote, the AWS cloud, and the Ignition database provides “real-time status,” according to Browne. This capability greatly improves operator productivity by enabling them to see the entire operation and interact with it from any location.
“Operators can see the big picture, which is significant when most of our work is in rural areas. If you are trying to start up multiple pumps at once or bring things up or down in series without exceeding pressures or overfilling pit levels, this gives you real-time information to support your decision making. Or maybe your tanks are getting low and you need to turn some pumps on to boost the supply, you can see exactly what you need to do and do it. This is IIoT the way it’s meant to be,” said Browne.
“You are just putting the whole process in the operator’s hand. The Ignition interface is very graphical, very easy to interact with the process. You can start or stop the pump, change speed, spot trends or check level or pump speeds easily. You can check the flow rate of any of those parameters across your entire line,” added Taylor.
A key component in that big picture is the ability to detect and respond to leaks.
Leaks happen
Leaks are unavoidable in above-ground temporary water transfer operations. How a water transfer company manages leaks can impact budgets well into six-figure totals.
“You’ve got trucks and vehicles all over the place, bumping up against your lines as they steer to avoid puddles or other obstacles. Leaks are inevitable and how effectively you can detect them and manage response can have a six-figure impact on operating costs. You risk the cost of lost water, repair, downtime and, because you often need to blend brackish waters, clean-up costs can also go into the six figures. If the leak occurs overnight, you could flood out a road before you know it,” said Taylor.
The Flow-Sync automation system provides continuous leak detection and intervention capability that is unprecedented in the water transfer industry. Its Max software monitors the line from beginning to end. Once the pump starts up, it takes about 10 minutes to achieve a steady-state of operation and the Max application at the other end of the line knows what to expect. A significant deviation, the software signals the Bedrock controller which might sound an alarm, shut the process or some segment of it or take other preset mitigation steps.
50 percent more productivity; reduced downtime
The complete automation system increases the productivity of water transfer operators by more than 50%. Where one operator might traditionally manage one or two pumps, the automation system enables a single operator to control an entire transfer operation (typically a second operator is kept in the vicinity as a rover) with even greater reliability and decision making.
And, because problems are detected immediately, costly downtime and leakage are minimized.
Reduced administrative costs
Automation that is both open and secure also helps drive down administrative costs, which can also be critical to profitability. As Taylor puts it:
“We are essentially in the business of selling water and so we must be able to track and monitor expenses and inventory accurately. We have to map expenses to projects. Without an automated system, if expenses come when you already moved on to another project, for example, you’d have to go back and find the paperwork, read the meters manually, map it to the appropriate particular project, etc.,” he said.
“Now we generate reports every day, essentially in real-time. We provide the data to bill or to reconcile, for royalties. We’re capturing all metering and flow rates into a database that we can make accessible for both our customers and water suppliers,” he continued. “From a single screen, we can control activity on any job site, commit inventory, or otherwise manage hundreds of thousands of gallons of water from multiple pit locations. This puts massive amounts of data in the hands of our operators,” Taylor continued.
A complete IIoT solution
Automating water transfer, the Flow-Sync systems boosts operator productivity in at least four ways:
• Real-time visibility into all operations to monitor multiple pumps remotely, giving each person control over a larger portion of the water transfer operations.
• Automatic leak detection, alarming and intervention, avoiding costs related to lost water, system downtime, clean costs, and potential fines.
• Reduced administrative costs in managing and reporting on water inventory and costs while also improving accuracy.
• Improved transfer design improves efficiency and reduces energy costs, which could be the highest cost variable for most transfer operations.
This successful collaboration among water transfer and automation specialists shows that great strides in water transfer productivity and cost control can be achieved with secure open technologies and the cloud. Given the current cost-cutting focus in the oil and gas industry, such efficiency improvement enables suppliers like FLOWPOINT to be more aggressive on pricing in competitive situations. Moreover, running this automation on a rugged Bedrock OSA platform with built-in cyber security shows that such gains can be achieved with negligible risk of cyberattack and high protection from environmental extremes.
For more information about reducing costs in the oil & gas industry contact Bedrock Automation.
___________________________________________________________________________________________________
**This post is a Sponsored content article. If you are interested in sponsored content on pbog.com please email pbog@zacpubs.com**