by Jeff Elliott
In all segments of refining and distribution, oil and gas facilities and pipeline stations regularly store and dispense large quantities of flammable and combustible liquids. Given the potential for gas, vapor, or dust to collect in these areas, the electronic equipment installed for automation and control must be designed specifically to prevent unintentional ignition of these elements due to electrical arcing or other thermal means.
Although much attention is given to the automation system components used to control the process itself, these systems also require computing equipment such as thin clients, panel PCs, remote touch displays, KVM (keyboard, video, mouse) solutions, and fixed and mobile operator workstations. Given the risks, this equipment must also meet the requirements for use in areas classified as hazardous and be rugged enough to withstand the harsh chemical and high humidity environment generated during the refining and manufacturing process.
“In the oil and gas industry, the manufacturing, processing, storing, and distribution of flammable materials release gases or vapors in the atmosphere which can result in an explosion or hazard. To create a safe and secure working environment, the computing systems at the worksite must, by regulation, be designed to pass the explosion-proof certification and be able to withstand the corrosive environment,” says Paul Shu of ARISTA Corporation, a provider of computing platforms and visualization display products including thin clients, all-in-one panel computers, ruggedized LCD touch displays, and industrial KVM solutions.
Ruggedized Computing Solutions for Hazardous Environments
In simple terms, a hazardous classified location is any area or building or commercial/industrial premises likely to be exposed to fire or explosion due to the presence of flammable gases, vapors, flammable liquids, combustible dust, and other similar materials in very high amounts.
Hazardous locations can be classified into various categories according to the nature of flammable vapors or liquids. In North America, a class/division system is primarily utilized, and regulations related to the design and manufacturing of industrial equipment are formulated by the NEC, CEC, OSHA, and NFPA (National Fire Protection Association). Outside of North America, a similar “zone” system is used to define and categorize hazardous areas and potential risk sources.
To meet the requirements of midstream and downstream oil and gas, as well as petrochemical industrial environments, there are several methods by which equipment can be made flame- and explosion-proof. For computing systems, equipment manufacturers that serve the market can design and manufacture thin clients, industrial panel PCs, and touch panel PCs that are UL certified, non-incendive (equipment having electrical/electronic circuitry that is incapable, under normal operating conditions, of causing ignition of a specified flammable gas, vapor, dust, etc. due to arcing or thermal means), and that meet the requirements for the various classes/divisions/zones within a plant or station.
ARISTA, for example, offers a wide range of panel mount and fully sealed touch panel PCs for the oil, gas, and petrochemical industry. The fully enclosed version is constructed of stainless steel and has no external vents. This design protects the components from gases, dust, dirt, moisture, chemicals, oil, and other external contaminants in an explosive environment.
According to Shu, the touch panel PCs in various sizes are routinely deployed as HMI workstations in automated tank farm and loading rack operations. In North America, tank farms serve as the primary distribution point for petroleum products that ultimately arrive at gas stations. These petroleum products typically arrive at the tank farm by pipeline or rail car and are then delivered to the tanks operated by various companies and agencies. Large quantities of products, primarily flammable and combustible liquids, are stored at these locations and are then distributed to service stations and other facilities by tanker truck.
For this type of application, the panel mount PCs are fanless, ruggedized systems certified for use in Class 1 Division 2, Class 2 Division 2, and Class 3 Divisions 1 and 2 hazardous areas. The systems are installed with a Windows operating system and the high-resolution touch screens can be manipulated by operators wearing heavy duty industrial gloves.
The company also offers fanless thin client versions as well, which are increasingly popular in the oil, gas, and petrochemical industry as a cost-effective way to develop a virtual desktop for more centralized management. With remote accessibility, it is easier to manage, store, and use the data, and IT administrators can conveniently access any device connected to the server and make changes. Moreover, thin clients are easiest to configure, manage, and deploy.
To maintain a completely safe industrial working environment, midstream and downstream oil and gas producers, as well as petrochemical product manufacturers, must install computing systems and peripherals that meet the industry regulations and security standards for hazardous locations across the globe.
By working with leading providers of computing platforms with experience in the industry, facility managers can obtain the UL certified, non-incendive, corrosion resistant thin clients, industrial panel PCs, touch panel PCs, and other critical equipment that will stand up to harsh industrial environments.
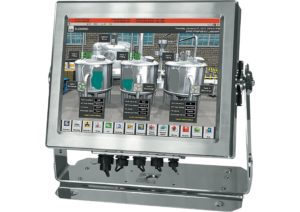
Shown here: an “industrial panel” PC from Arista. By working with providers of ruggedized computer systems, facility managers can obtain critical equipment that will stand up to harsh industrial environments.