The oil and gas industry has historically evolved as a business sector that welcomes the implementation of innovative ideas and then makes the most of the ensuing improvements. Much like compounding interest in the financial sector, drilling mud technology has undergone improvement, with the next best idea building on the previous.
While oil-based drilling mud has long been the industry staple, new techniques offer a vast array of solutions, and those seem to circle back and tap into their own roots. As synthetic and water-based muds have grown in popularity, direct emulsion might just be the next important thing circulating within the Permian.
Responding with R&D
While the catalyst to find innovative solutions in drilling mud technology comes mainly from the push to be environmentally friendly, some lessons from the recent past can prompt us to take a wider view. According to James Dennis, petroleum consultant with Dragonslayer Engineering, the oil and gas industry suffered a blow in 2008 when the country’s political landscape changed.
The oil and gas industry was under scrutiny, but instead of applying millions in allocated funds earmarked for drilling and completing wells, companies redirected those funds to research and development. Drilling mud technology was at the forefront of experimentation, with synthetic-based solutions taking precedence.
“It was around 2008 that companies started experimenting with oil-based mud and reclamation,” says Dennis. “They were reclaiming nearly 90 percent from the cuttings, and they could release, but it was very expensive.”
The focus on synthetic-based muds captured interest, and like all other areas of the oil and gas industry, it became the starting point for expanding ideas and viable concepts. Water-based muds would also evolve, and then interest would revisit further development of past models like direct emulsion.
Overcoming Method Challenges
The challenges associated with drilling mud dictate the solution used in each specific application. Mud and drilling fluids play a critical role. They are tasked with controlling formation pressure, removing cuttings from the wellbore, lubricating and cooling the drill bit, preventing formation damage, preventing fluid loss, and minimizing corrosion.
“The type of hole you are drilling, or the phase of the operating you are completing, will help you determine the proper fluid system to use,” says Mike McGraw, who manages MMP Consulting.
According to McGraw, selecting the correct mud or drilling fluid ensures that the formation does not suffer damage during downhole operations. The correct application additionally assists in maintaining wellbore integrity while avoiding swelling or sloughing from within.
“The drilling fluid must remain stable when encountering various contaminants such as gases, salts, solids, and higher temperatures,” says McGraw. “These contaminants could make it challenging to maintain these critical wellbore characteristics.”
McGraw says that to combat challenges that threaten drilling operations, much attention and study are directed at the wellbore to guide professionals in selecting the correct mud solution. The more attention given to the operation before going downhole, the better.
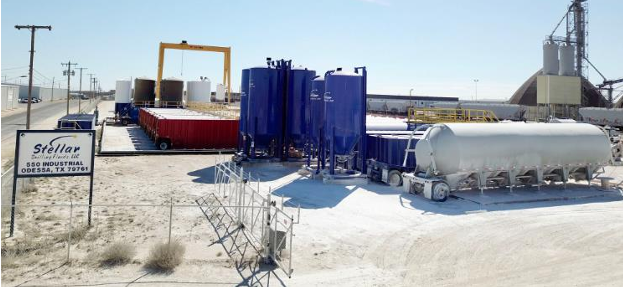
Stellar operates a large yard situation on a rail spur in Odessa. This facility is at 550 Industrial.
“To ensure we avoid any possible train wreck or contamination that could result in a high cost well, we do several things in the front,” says McGraw. “We study offset well data, compare our TVD lateral benches to the other operator TVD lateral benches, and perform multiple daily checks of various properties such as pH, density, rheology, alkalinities, and other properties.”
According to McGraw, companies perform pre-drill testing to select the correct mud solution so the mud does not experience any wellbore swelling. This provides the framework for choosing a more inhibitive water-based mud system and switching to an oil-based mud alternative.
“One of the biggest issues I see when working with certain fluid companies is the lack of tracking the data,” says McGraw. “If data is captured and filed away to easily become searchable from now to the foreseeable future, then we can begin to provide the service that each oil and gas operator should receive when hiring a fluid company to provide drilling fluid services for them.”
Implementing the Correct Solution
In addition to the characteristics of a wellbore, the emphasis on cost plays a significant role in choosing the correct drilling fluid system. McGraw says more quality, high-performance water-based mud systems can withstand bottom hole temperatures of 300 degrees Fahrenheit and up. This provides a viable solution when analyzing the costs of using this application over an oil-based mud system.
“On both the drilling and completions sides, we are seeing more and more tools that can handle higher flow rates,” says McGraw. “This allows us to achieve higher annular velocity, which is a big component in cutting, transporting, and removing from the wellbore.”
Here, the environmental factor has waged its own influence on drilling fluid selection. Jay Manning, engineering manager with Stellar Drilling Fluids, says that while oil-based muds have been the comfortable staple of drilling fluid selection, the push to eco-friendly alternatives and more efficient solutions is growing.
“You have standard oil-based drilling mud that most old-school drilling mud engineers want to fall back on because it is considered fool-proof, but now the industry is moving to a synthetic-based mud system, or you can call it direct emulsion,” says Manning.
Oil-based mud is typically diesel-based, so it carries environmental concerns. The synthetic-based option can be mineral-oil-based or feature a synthetic hydrocarbon. Both are more environmentally friendly, exerting no negative impact on the land or wildlife. Although the “green” theme has held sway in the oil and gas industry, the factor of higher costs comes with it—and brings its implications for decision-making. As a result, water-based mud solutions have grown in popularity within the Permian Basin.
“We are using clear water with a lubricant package, and we are able to drill two- to three-mile-long laterals just with that alone,” says Blake Whitter, Stellar’s Permian Basin operation manager. “Hydraulics are used to clean the hole and the lubricant package for lubricity and pipe wear.”
Whitter adds that the post prevalent concern associated with using water-based mud—drill pipe torque and pipe wear—is simply the trade-off when using the water-based system over mud.
“A pound of oil-based mud weighs the same as a pound of water-based mud,” says Whitter. “That weight affects the wellbore in the same manner no matter the medium used.”
He adds, “Water-based mud offers a more economical solution if it is used correctly. The benefits include the lack of a large diesel bill associated with oil-based muds and the fact that you avoid reclamation costs.”
Manning and Whitter see the need to compare water-based and oil-based mud applications. Environmental concerns must be compared to oil-based mud costs. What each operator finds important must be compared to budgetary restraints.
“You’ll spend more money on lubricant in a water-based mud system that you wouldn’t spend using oil-based mud, but it is one-fifth the cost of the diesel,” says Whitter. “Looking at the big picture, you have to weigh all aspects to see if a water-based mud solution is more economically viable, but typically it is.”
Advancement Through Compromise
Depending on whom you ask, arguments can be made in support of each application when it comes to water-based and oil-based mud systems. The need to be eco-friendly is growing, but cost will always plague an operation. Water- and oil-based mud systems offer positive attributes with their own challenges.
“I see a big move to high-performance water-based muds emulating oil-based mud, especially when it comes to drilling pipe wear,” says Whitter. “It’s better for deeper and longer laterals.”
In the spirit of transition, Manning and Whitter point to a compromise solution known as direct emulsion. With oil-based mud, diesel is emulsified into water.
“So you work with a ratio, and it would be like 80 percent diesel and 20 percent water,” says Manning. “With direct emulsion, you flip that to 20 percent diesel and 80 percent water.”
Manning adds, “You’re still getting the lubricity from your diesel or whatever oil medium you are using, but you’re not having to use as much.”
The simplicity derived from that ratio proves vital in reasoning its benefit. The environmentally friendly aspect is maintained by reducing the use of diesel or products potentially harmful to the land or life forms while working within the limits of budgetary constraints through limitation in oil use.
According to Manning, Stellar has provided several direct emulsion solutions throughout the Permian Basin, all of which have achieved successful results. Their use, however, has yet experience a leap forward, unlike breakthroughs in other aspects of the oil and gas industry. While this breakthrough may solve economic challenges, the lack of adoption may be due primarily to economic factors.
“Most have oil-based mud systems pre-built and ready to be deployed to the field,” says Whitter. “Direct emulsion is not in high demand yet, so those systems are not readily available. As a result, mud companies would likely pass those systems’ build costs to the operator.”
Whitter points to direct emulsion growth potential when a customer has long-term work and will be drilling multiple wells. The costs of building a direct emulsion system could then be spread between all the wells scheduled for drilling. Until that happens and the cost of diesel remains at an acceptable price, direct emulsion systems are less likely to be used. Whitter, however, sees the potential coming, especially with the demand to exercise good environmental stewardship and go green.
“We had a client that wanted to go with a synthetic mud solution,” says Whitter. “They wanted to go green but didn’t like the costs associated with the application. Direct emulsion would have been a great alternative. Especially with these types of situations. It is only a matter of time before direct emulsions become a more viable and popular solution used here in the Permian.”
Nick Vaccaro, owner of Vaccaro Group LLC, services the energy industry as an HSE consultant and freelance writer. A contributor to numerous industry publications, Vaccaro holds a BA in photojournalism from Loyola University. He can be contacted at 985-966-0957 or nav@vaccarogroupllc.com.