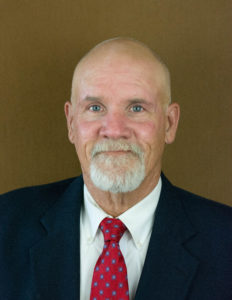
Dusty Roach
Greetings and salutations! I am excited and optimistic for the New Year. Each year everyone shares this common enthusiasm to celebrate the previous year if the safety performance has been deemed successful and injury free. Conversely, if the company has experienced a less-than-stellar performance, there is still much relief that comes from embracing a needed reset and start to a new year. As is true for everyone on New Year’s Day, there is optimism for the New Year, with all kinds of new year’s resolutions and renewed vigor. Unfortunately, the new year’s resolution (corporately) lasts as long as most individuals’ resolutions; which for me personally is about 30 days into the New Year.
There are specific ways to overcome this phenomenon, but as usual it requires a company and/or individual to have proper planning and execution. Without identifying where the weaknesses are, the plans also become an early disappointment, similar to the resolutions. So where do we start?
My recommendation is “let’s start at the very beginning.” That ought to be a song. I digress. Regardless if you have new hires with experience, or new hires with limited or no experience, they sit in the same new hire training class. Both types—experienced and less-experienced—are already misplaced and both will suffer before they get started. The suffering will be largely due to the cookie-cut “new hire” training that is ready to “herd out” as many new hires as possible.
I am not insinuating that any entity or company is taking short cuts. However, to pretend that one size fits all is ludicrous. The new hires may be sharp as a tack, the instructors/trainers may be brilliant, and the material is typically competent, but to suggest they have had adequate training is less than likely. The experienced hands usually sit in the back, looking at their phones doing what I used to call the Blackberry prayer. The “new to the business” new hire has a glazed look in his eyes, wondering what in the world he got himself into. Then, when we start talking about equipment, slang terms, and policies and procedures on 8-10 required subjects squished into 8 hours, they are knotted up tighter than Dick’s hatband.
So, what do we do? Here is what I propose. By this time I contend that we have at least two different types of new hire classes: 1. a class syllabus for the experienced new hire employee, 2. another, different syllabus for the new hire person often referred to as a “worm.” This simple, yet hard-to-execute plan, is convoluted further by the workforce speaking English and/or Spanish. Overhiring is not usually feasible nor recommended for most companies, as we all have budget concerns. Qualified bilingual safety instructors are recommended.
For the experienced new hires, the training should be more advanced, with sharing of experiences that were contrary to the norm. I recommend classes that are condensed in class time with next-level information examinations and a thorough remediation of incorrect answers. Additionally, “advanced” new hire classes provide an opportunity for input, feedback, and questions of how they perceive processes could be bettered. It also promotes a learning environment and leads to input that can potentially get better buy-in from bottom to top.
For the “new to the business” new hires, run a standard class of all the minimum requirements by law. Having smaller classes will help the ones who otherwise might struggle. Further, it will help the instructor to identify behaviors, and to instill overall comprehension of the material, in addition to achieving better performance on the standard required tests. If your goal is to simply get the new hires through the oilfield training combine, and get them into the field, you have yourself a recipe for (unfortunate) incidents.
From experience, I can tell you that the emphasis on new hires is achievable and even should be paramount. The overall goal should be to more than adequately prepare the new hires to gain a complete understanding of the importance of safety. If your goal is just to be documented by taking a one or two day class, then administering multiple “guess” tests, remediating the answers, and getting documentatin that your hires have passed the minimum standards, then good luck. I prefer not to rely on luck when it comes to safety. I contend there is no bad luck, just poor planning, poor preparation, and/or poor implementation.
We that are long in the tooth have learned from experiences, some good and some that are really bad. My “takeaways” don’t always apply to every situation. My passion and perspective for safety applies to every job and every situation. Training, certifications, and degrees are recommended. Every time I see a new hire, I feel it is my responsibility to ensure that they know the risks and know safety, and that they visibly recognize the passion that we have for their welfare. Happy New Hire! Happy New Year!
And as usual, like baseball, it is not how many big hits we have in life. It’s how many times we reach home safely!
___________________________________________________________________________________________________
Dusty Roach is a safety professional based in Midland. He is also a public speaker on subjects of leadership and safety, and he maintains a personal website at dustyroach.com.