With the tidal wave of disruptions over the last two years, the oilfield service sector has had to pivot, reboot, and refocus just like the rest of the industry. Midland-based Forty A&M LLC specializes in shooting fluid levels and well optimization, and California-based Tetra Tech’s Permian business mainly consists of treating and handling produced water. Here are their stories.
From Majors to Mid-Size
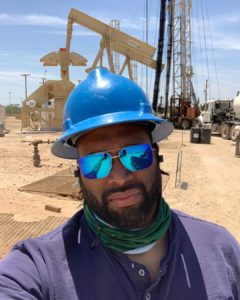
Joseph Norman
For Forty A&M founder Joseph Norman, the years 2016-2019 provided a predictable workload. His clientele included much business from large independents, along with midsize and smaller companies. “In March, 2020, that all changed. It went from me being on monthly schedules for servicing clients to just an as-needed basis. That pretty much happened overnight,” he said.
Around September of 2021, things began to pick up, as Norman received more calls—still for as-needed work, but at least it was needed more often than it had been for the previous 18 months.
The biggest difference is that many former clients—mainly the larger ones—decided to hire staff to do the fluid level surveys and dynamometers they’d previously contracted with Forty A&M for. “That changed who I am marketing to. I’m really not marketing to large companies any more—just small-to-medium size companies that are not hiring their own well technicians, that are still contracting that position out.”
Norman admits that his potential client pool has thereby shrunk, but feels that “there are still plenty of opportunities among those small-to-medium size companies.”
Most calls now are for shooting 5-10 wells one-off instead of the 150 every month of 2016-19’s halcyon days. These numbers reflect the reality of smaller operators, not large enough to need or afford a full time well technician.
Branching Out
As another part of his rebooting, Norman plans to buy a few oil wells to operate. “I’m pretty excited about that, I’m sticking my neck out,” he said, adding that he wants to jump on opportunities when they arise because the future is uncertain anyway. “You might as well go for it right now and see what happens.” If it doesn’t work out, “You just get up, brush yourself off, and keep moving.”
On the positive side, “Having a barrel of oil at $80 ain’t bad. You gotta strike while the iron’s hot.”
A History in Oil and Glass
Norman grew up in Midland in the oil and gas business. He and brothers John (now a Midland city councilman) and Josh were well documented in area sports reporting in the late 1990s, helping what was then known as Lee High School to three consecutive state football titles.
Their father, Jerry Lee Norman, began a career with Exxon in the 1970s as one of the company’s first affirmative action hires. “That’s the only reason he got an opportunity, is because of affirmative action,” Norman said.
“He started out on a well service rig on a 15 degree day in a silk shirt because he had no idea what to wear on the rig.” It ended up working out, as the elder Norman spent 20 years with the company, until “He felt like he hit the glass ceiling at Exxon, and he went out on his own as a contract lease operator.” Joseph added, “I still have his hard hat from Exxon.”
Once his father started his own business, the younger Norman recalls being dragged out of bed at 6:00 on summer mornings to work alongside his father. “Really, I’ve been out in the oil field for the last 25 years, whether it was cutting and threading pipe, gauging tanks, checking gas meter runs, I’ve been out in the oil field with my dad.”
Joseph returned to his father’s business after college. Soon after the elder Norman passed the business to John, after which Joseph stayed on for about a year. “Me and my older brother John are the only ones that are in the oil field,” said Joseph. “Josh didn’t want any part of the oil field.” Instead, Josh stayed with football and is head coach at a high school in Oklahoma, where he played college ball.
He founded Forty A&M in March of 2012, along with his wife, Belinda.
Picturing the Future
In addition to buying some wells, Norman has two other forward-thinking options. One that he’s already working on is automating the fluid levels and greenshots. Installing those systems on wells allows the data to be collected without a trip to the well.
Forty A&M will still be needed to record and interpret the results, so the business will be able to continue at that level.
Second, Norman is using his photography and videography skills to help companies around Midland. And he has larger plans. “What I want to do is provide content for oil and gas companies. I feel like, especially with this administration, there is a trend away from oil and gas.” Despite pushes toward wind and solar, Norman feels oil and gas is still vital.
“But we have a bad rap, and that is partly our fault.” He wants to help companies promote the positive side of the industry, while encouraging the industry itself to do more to clean up its act.
Keeping Up with Changes in Water Midstream
The average Permian Basin well produces 8-10 times as much water as oil. As many stories as there are about takeaway capacity for oil, gas, and NGLs, the requirements for water handling dwarf all of those.
For TETRA Technologies, the changing landscape of water recycling has fostered systemic changes. Among those are new ways to deal with sand in completion fluids as companies switch to softer (lower crush) local sand to save costs.
Recent Texas Railroad Commission-issued restrictions on SWD activity near Gardendale, north of Odessa, have caused producers to do more recycling, said Coby Reynolds, Chemical Engineer at Swiftwater, A TETRA Company.
He explained that the RRC’s ruling temporarily restricted allowable volumes to 10,000 barrels per day, about half the usual permitted rate. “So we have seen an uptick in requests for large-scale water recycle facilities in the Midland Basin.” Requested flow rates of 2-400,000 barrels per day—far beyond historic levels in the area—are now being requested.
Sudden, on-the-fly adjustments are commonplace in Permian Basin produced water issues, he said, adding, “It’s a perpetually moving target as far as how much you treat and where customers want their KPIs [key performance indicators] to be.”
Treating water to comply with specifications is the easy part, Reynolds said. The bigger challenge with increased flow lies in finding storage space to hold those volumes while the water waits to be used. “You’re feeding two or three frac pads with 100 percent produced water. Insuring that those simulfracs aren’t cut short of water—the primary component of any frac job—becomes a challenge. Really it’s just a logistical question. We haven’t yet faced any obstacle we haven’t been able to meet.”
As in almost every industry since the Pandemic, water recycling faces supply challenges in getting enough treatment equipment in a timely manner. Plus, whether by mandate like the Gardendale situation or through other stimuli, the industry is rapidly embracing water recycling like never before, creating even more demand for equipment.
Due to the increased demand, the company had to get creative with sourcing equipment, having recently boosted their in-house recycle technology development.
TETRA has also received new business from E&P-owned water midstream facilities looking to expand recycling facilities during the Gardendale restrictions, which may or may not be temporary. Reynolds noted that those midstreams were outsourcing the extra capacity to his company, possibly because they were hesitant to invest in new equipment, personnel, and infrastructure to handle a possibly temporary situation.
The flood of requests for new and higher-capacity facilities is keeping Reynolds and his Permian Basin group busy. “We are very much in a new era of recycling. In past days, not even eight years ago, 50,000 barrels a day was considered a lot of recycled water for one operation. Now, that’s just the starting point.”
Sand Capture
As operators strive for cost reductions in all phases, many have switched their frac sand to locally-sourced types rather than the previous gold standard of northern white high-crush sand. While this saves greatly in transportation, the softer Permian sands that start at 100 mesh often turn to powder in the completion process.
Smaller mesh does have some economic benefits in the completions process, said Adam Calvin, Central U.S. Production Testing and Fluids Manager. “However,” he added, “when you bring that well online and get those frac fluids back and start producing that well, some of those solids come back. They’re much more difficult to manage than the larger solids that we’ve seen historically.”
The additional issue of lower crush strength of in-basin sands was seen as further taxing current sand removal systems. “Technologies on the market today weren’t capable of capturing those smaller solids,” Calvin said.
TETRA then reviewed a number of existing technologies to see which one was best suited to being updated to handle the smaller sand particles. “So our engineering team determined that a properly sized hydrocyclone could effectively separate these particles.”
TETRA evaluates particle size and flow rates to ensure the proper amount of force is applied to separate the particles from the liquid stream.
Branded as the TETRA SandStorm™ advanced cyclone technology, the unit is modular, with a number of inserts that can be interchanged depending on what each well needs.
Field trials began for the unit in 2018, with full production starting the next year.
It sounds like a Max Headroom glitch to keep saying that change is survival these days, but those reminders are everywhere, including the companies included in this story.
______________________________________________________________________________________________
Paul Wiseman is a freelance writer in the oil and gas sector. His email address is fittoprint414@gmail.com.