MWD technology has transformed the drilling industry, taking an impossibility—horizontal drilling and its related technologies—to successful new heights, er, depths.
By Al Pickett, special contributor
New technology has revolutionized the oil and gas industry, helping companies find new hydrocarbons and drill wells most efficiently. There may not be a better example of that than the phenomenon of Measurement While Drilling, better known as MWD, which was first used in offshore drilling and is now a requirement for drilling horizontal or directional laterals onshore.
Jason King, MWD coordinator for Wellbenders Directional Services, LLC, said MWD is like working off of a plan or blueprint when building your home. “It allows you to stay in the window,” he stated. “The advancement of MWD from 10 years ago to now is amazing. The technology is through the roof with the information you get.”
MWD is a system that was developed to perform drilling related measurements downhole and transmit information to the surface while drilling a well. MWD systems can take a number of measurements, according to King, including natural gamma ray emissions, directional surveys, tool face, borehole pressure, temperature, vibration, shock, and torque, etc. King said his responsibility includes the Permian Basin and Eagle Ford Shale plays in Texas for Wellbenders, which is headquartered in Conroe, Texas, but also has a facility in Midland.
Mya Cardenas, business analyst for Boreview Services, compared the MWD tool to a GPS (Global Positioning System) in your car. “The GPS gives you a Point A and a Point B, but you as a driver guide the car between those two points,” she explained. “With MWD, Point A is the surface and Point B is the downhole target. The MWD always lets you know where you are at and the information helps fine-tune your path. It is not possible to drill a horizontal or directional well without MWD because you will not be able to tell where you are. It is like your eyes downhole.” And the MWD tool is wireless, and could be one of the following technologies: positive pulse, negative pulse, or electromagnetic wave transmission, according to Cardenas.
Boreview Services, located in Stafford near Houston, is a service company that provides DD (directional drilling, MWD, and LWD [logging while drilling]) services. “Our engineers have been working on probe style MWD and LWD systems for more than 10 years,” said Cardenas. “We can handle the world’s toughest drilling and measurement jobs using the best proven technology in the industry to provide services and solutions to our customers. We have operated in over 100 jobs worldwide and in different continents such as North America, Asia, and Africa. Additionally, we have completed jobs all across the United States, including Texas, Oklahoma, California, Wyoming, and many more states.”
Cardenas cited an example of a well in the harshest of conditions that Boreview was able to help a company drill with its MWD tools where older technology wasn’t able to do so.
“A customer was drilling a wildcat well in Jefferson County [in southeastern Texas],” she recalled. “They had been drilling for two months before we arrived. They were drilling with old technology, using a steering tool which is like a wireline MWD. The pressure was over 15,000 psi and the temperature was 340 degrees. Not a lot of MWD tools can withstand that situation. They would drill a little bit and then put the steering tool down the hole and take a survey, then drill a little more and repeat that process. In one week, they had drilled only 100 feet. The owner was upset, and he called us. We looked at it as a challenge. We ran some calculations and believed that this was a job we could successfully complete, and within the first 24 hours we had drilled more than 100 feet. We were there five days in extreme conditions. We took a lot of pride in that because one of the top three service companies was there and their tool couldn’t operate in such conditions.”
Cardenas said that using MWD tools is required to drill horizontal or directional laterals to make sure the driller is hitting his plan in the targeted formation. It is also important in pad drilling to make sure one doesn’t drill into an adjacent wellbore. She noted MWD is also used in drilling some vertical wells that require directional correction. “But while building the curve, you need the MWD tool in the hole,” she maintained.
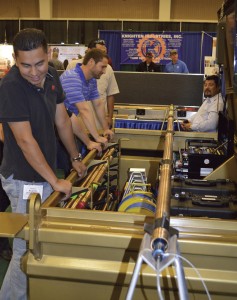
The exhibit of MWD Supply, a local leader in MWD tools, was a favorite with attendees at the 2014 Midland Energy Expo held in April at the Horseshoe Arena in Midland.
So How Does It Work?
King said MWD tools are conveyed downhole as part of the bottom hole assembly that includes the mud motor, stabilizer, and universal bottom hole orientating sub, as well as the drill bit itself. The MWD tools are either contained inside a non-magnetic drill collar or built into the collars themselves. MWD tools use accelerometers and magnetometers to measure the angle or inclination that the bit is drilling as well as the azimuth or hole direction of the wellbore at that location. “The tool is about 30 to 50 feet behind the drill bit,” he explained. “The mud motor has a slight bend in it. The bend in the mud motor is lined up with the tool face. By turning the tool face, it allows the driller to steer the direction of the bit. The MWD tool updates the information it is sending every 14 seconds. That allows us to read it and interpret the information for the client or directional driller. It measures natural gamma ray emissions from the rock, and that is sent to the geologist to determine the type of rock formation being drilled. It also helps the driller determine what direction to turn the bit. It allows you to reach the target or pay zone faster.”
King explained that the MWD tool measures the trajectory of the hole as it is drilled. Using basic trigonometry, a three-dimensional plot of the path of the well can be produced. This information is then used to drill in a pre-planned direction into the formation that contains the oil, gas, water, or condensate. Directional drillers rely on receiving accurate, quality-tested data from the MWD engineer to allow them to keep the wellbore safely on the planned trajectory. Certain MWD systems have the capability of receiving encoded control commands, which are sent by turning on and off mud pumps, changing the rotation speed of the drill pipe, or by other advanced telemetry technology such as wired pipe. Of course, all of these measurements are taken in real time. “Since the sensors are in the hole while the drilling is taking place,” Cardenas added, “anytime the directional driller wants to take a survey, we can provide one. Surveys are almost instantaneous these days as technology gets better.”
Although MWD technology first began in the 1970s, Cardenas said it became more and more useful in the late 1990s and then its use became even more prominent in U.S. onshore operations in the past decade, as horizontal drilling took over in the nation’s resource plays. She pointed out its first major onshore use was in Colorado in the directional drilling of methane wells. Using MWD technology also saves money because it saves time, according to Cardenas.
“It has changed the industry a lot because now drilling is faster and cheaper,” she contended, “and you conserve a lot more time because our measurements are reported as the well is being drilled. All of the information that you need to drill and steer the well are downhole, unlike the early days of directional drilling when they had to stop and drop single-shot or multi-shot type surveys. Because the information is readily available to you in real time, the directional drillers are using the information to steer the well according to the pre-planned well plan, and the geologist is looking at the gamma ray measurements to ensure that they are in the reservoir of interest by comparing the data to previously drilled wells.”
Accuracy Required
Companies such as Boreview Services or Wellbenders not only supply and maintain the MWD tools, but they also provide engineers to be on the well site to properly interpret the information being transmitted from the downhole tools. “Every measurement that you collect during the surveys must be accurate,” Cardenas stated. “If you give the directional driller the wrong information while he is trying to trying to drill the well, then things can go very bad very fast. You have to be vigilant and make sure that you keep your eyes on everything that is going on at all times.”
Horizontal drilling and hydraulic fracturing may have revolutionized the oil and gas industry in the past decade, but the technological advancement of Measurement While Drilling systems has made horizontal or directional drilling not only possible but also successful.
Al Pickett is a freelance writer in Abilene and author of four books. He also owns the West Central Texas Oil Activity Index, a daily and weekly oil and gas reporting service. For more information, email apickettc@sbcglobal.net.