Power. Producing power is what the energy industry is all about. And power is what feeds the energy industry, primes its pumps, lifts its resources, and keeps drillstrings and driveshafts turning to the right.
Portability. Portability is what energy producers are all about. It’s a pick-up-and-go industry. Nothing stays still for long. Other industries have their static, immobile ways. Manufacturers have factories, publishers have presses, food processors have their plants. But the upstream oil and gas world goes where the next zone beckons.
That’s why the pursuit of power, and the pursuit of portability, are the eternal verities of the oilfield. That’s why new iterations are always forthcoming on these themes. There’s always a new generator, a new compressor, new engine, new pump… the list goes on.
We checked in on a couple of professionals in this space and learned, well, what we suspected. Which is that change happens, and happens fast.
Mike Postel is president of Connexa. Based in Comfort, Texas, Connexa is a manufacturer and distributor of remote and industrial energy products, as well as an integrator of IioT(Industrial Internet of Things) products. The latest change for Connexa is the launch, in August, of its new package that it calls a “hybrid power skid.” Fully stand-alone, these hybrid skids provide autonomous power for SCADA, valves, pumps, and more.
In a conversation with this publication in August, Postel remarked that the new skid simplifies matters out in the field.
“We [Connexa] provide both primary and backup power, in general, for field electronics and automation,” he said. “So, with a hybrid skid, you basically have solar as primary power, and then there’s a backup generator that’s fueled by either propane, natural gas, or diesel. And there’s automation on board that regulates when the generator comes on, and when it does, it will recharge the battery.”
The generator can also be routed to supply power directly to start a pump or run a large motor or some other application, should the need arise.
“What the generator does is allow you to do is reduce the number of days of autonomy you [would need to] have in a battery bank,” Postel said. (Battery autonomy is defined as the period of time a UPS [uninterruptible power supply] batter will last at a specified load level, in the event of a power outage.) “So, on a small system, you wouldn’t see many generator backups because we can prettily easily span the days required for it to keep the system alive 24/7, 365. It’s when you get into a lot larger system that the economics change. Then it makes a little bit more sense to go to a system with a backup generator to reduce some of [the need for that] large battery autonomy.”
Postel said that lithium battery technology, which has improved significantly, has been a game changer.
“Back in the day, oil and gas was using solar, and doing so long before solar came into wide use in other industries,” Postel said. “The oil and gas industry has been the pioneer in solar power systems. A lot of people don’t know that.”
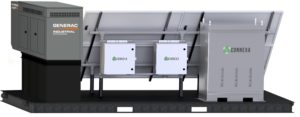
Shown here is one of Connexa’s new hybrid power skids. Connexa’s onboard battery banks, charged by solar, can provide up to 480V 3 phase AC output. These skids fully integrate UPS DC power, solar charging, generator interaction, motor controls, SCADA, power distribution (DC and AC), and data harvesting via IIoT or SCADA topologies.
Connexa’s customers fall in the large-end-user bracket, on the production end, rather than the exploration end, of the spectrum. Postel explains: “On the drilling side, businesses require so much power that it makes more sense for them to do everything off of large generators. But after they complete their [efforts] and production’s good, you’re into the long-term life cycle that we associate with the production of the well. There, these units of ours make a lot more sense economically. They are low-to-no maintenance. They get the job done pretty well.”
Connexa’s partnership with Generac allows for advanced configuration and product support in not only power, but accessing the field data with onboard electronics. Generator options include both natural gas and diesel, with the ability of Connexa to integrate up to 300kW models.
“Our skids are popular because you put it in place and it’s ready to go,” Postel said. “You literally just put it on the ground and it’s self-balancing. Set it on the ground and turn it on, you’re up and running.”
Postel said that the trend of battery technology, especially lithium batteries, across several industries, has been interesting. “And that, along with a lot of the environmentally green initiatives, is causing a lot of pressure to do more solar and more green technology in general, especially in oil and gas. There is a lot more monitoring.”When solar is brought into a system, its primary job is to charge the battery, he said. “And with the lithium technology becoming better and better, it’s going to be interesting to see far that trend goes. I think that oil and gas is going to be adopters of that technology. The price has come down, too.”
He added that the chemistries that are most common in oil and gas are “more of an AGN or a gel. Those are typically five-year batteries.”
Asked where he would like to see things go in the oil patch, Postel said he would like to see more wells get drilled. “The price of oil is pretty good, and we’re seeing activity, still,” he said. “But it’s not the level of activity we’ve seen in the past when we’ve had high prices like these before. We’ve stayed steady, though. At the end of the day, no matter what anybody’s doing, they’re increasing their power needs over time. And so, even if there are few new projects, there’s always just more and more power being added. It’s being added even at existing sites that haven’t added equipment. Because of that, we’ve stayed pretty busy, even in a slower year.”
Another place where the crew has stayed busy is Shale Pumps LLC.
At Shale Pumps, the impetus is always the same. More horsepower. Frac pumps are their specialty.
Jason Williams, vice president and director of engineering at Shale Pumps, said, “What we’ve been doing here is pushing the horsepower envelope.”
Their most advanced model, so far, is a unit that generates more than 7,000 horsepower. It runs most efficiently on natural gas, though it can run on diesel.
“When I say that we rate it at 7,000 horsepower, I’m saying we conservatively rate both the pump and the system 7,000 horsepower,” Williams said. “The aim is that the engines in midsummer, in West Texas weather, will shove out between 7,200 and 7,300 horsepower. In winter, those engines are going to shove out somewhere between 8,600 and 8,800 horsepower. The pump is robust enough and beefy enough to be able to handle both of those two ratings, during either [weather] condition. Keep in mind, they’re not going to be operating on the hottest day all the time. And you’re never going to be out there on the coldest day all the time.”
For comparison’s sake, a typical trailer-mounted frac’ing pump is a 2,500 horsepower quintuplex unit, powered by a 50 or 60 liter diesel engine that runs through a transmission. These units are typically 43 feet long, eight foot wide. They weigh right under 120,000 pounds. One 7,000 horsepower Shale Pumps unit delivers nearly as much horsepower as three conventional trailer units, and the Shale Pumps unit fits on just one trailer.
That makes a difference where frac spread footprints are concerned. If, say, a frac job requires 50,000 horsepower of pressure pumping, then that calls for about 7 of Shale Pumps’ 7,000 horsepower units. Versus as many as 20 pressure pumping units, if those are the convention type.
The Houston-based business employs only about 12 workers. The Permian Basin is the biggest market for their work.
Williams quipped that Shale Pumps is a “boutique” operation. But the label fits, in that, “We do custom jobs for a variety of businesses who need custom applications.”
Williams’ grandfather, Ellis Williams, started a company called EWCO, which pioneered some advanced mud pump designs. The company was bought by LeTourneau. LeTourneau is now one of Shale Pump’s bigger clients. After the purchase of EWCO, it was renamed LEWCO, and eventually became LeTourneau Drilling Systems. At that time, the business concentrated on higher horsepower mud pumps.
Today, frac pumps are where Shale Pumps puts its emphasis and where Jason Williams spends most of his development time. “One of the things that I’ve been doing is developing higher horsepower fracturing pumps, because I see the need, essentially, for consolidation in fracturing pump fleets, as well as the need for higher horsepower applications within that market,” he said. “We’ve been pushing higher horsepower frac pumps into the industry.”
Williams said the industry is going to higher horsepower frac’ing for a variety of reasons. One, to clean up emissions. Two, it’s more cost effective, in that your footprint on site shrinks, your personnel costs shrink, longevity of equipment goes longer, compared to conventional. So it does lower cost, and it lowers the cost of horsepower produced.
There are two costs to consider in frac’ing. “You have the initial purchase price, and then you have the cost of horsepower produced over the lifetime of equipment,” Williams said. “By going to higher horsepower units, you could drastically lower that cost of horsepower produced, over the lifetime of the equipment.
“We service a variety of industries,” he said. “We still manufacture the family’s traditional triplex, as well as quintuplex design, for drilling applications. Our drilling pump horsepower range runs currently from a 150-horsepower triplex on the small end, up to a 4,000-horsepower quintuplex drilling pump. And these are all Williams-style pumps, because my work simulates my grandfather’s work, because I apprenticed under my grandfather.
So far, it has all spelled success for Shale Pumps. Asked what it takes to succeed in the Permian Basin, Williams doesn’t hesitate: “Good relationships, good customer service, and a high quality product.”
____________________________________________________________________________________________________
By Jesse Mullins