The entity known as a “disposal well” is a vital element in the oil and gas industry, one that is not so well understood as it should be.
By Hanaba Munn Welch
If oil and gas wells had an official pecking order, saltwater disposal wells would be somewhere at the bottom of the list. They take the refuse of the oilfield, specifically unwanted saltwater that’s a byproduct of plumbing the earth’s depths for hydrocarbons.
Disposal wells may not be glamorous, but they are generally successful. They are fee-charging income-producers, or cost-savers, depending on ownership. For decades, they’ve played their unassuming roles, mostly out of the spotlight but important because they handle unwanted produced water, also called brine.
In today’s oilfield, technological developments in water and fluid management reflect a high-profile trend toward recycling and reuse. Even some disposal wells are getting caught up in the action, benefitting from new technology. Case in point, Fort Worth-based Bosque Systems, LLC, touts its proprietary water treatment system, DIONIX by name, as a way to upgrade disposal well operations.
“We have two different DIONIX lines,” said Scott Crawford, spokesman for Bosque. “The mobile DIONIX unit goes out to the actual site and treats the water for hydraulic fracturing. The stationary treats the water at saltwater disposal sites.”
Why treat for water destined for disposal?
Because it’s not just saltwater.
“Water going down hole can contain high bacteria, high hydrogen sulfide or iron sulfide,” Crawford said, citing elements that can compromise a disposal well. Oxidation, for instance, can result in higher injection pressures that can harm the formation itself.
Treating the water before it’s injected into a disposal well is an expense subject to cost-versus-benefit analysis, whether the system is state-of-the-art (like DIONIX) or less sophisticated. Ask anyone who works on disposal well pumps.
“You can tell an operator who uses chemicals to treat their water and who doesn’t,” said Chad Keesee, operations manager for Recovery Equipment, a pump sales and service business based in Abilene. “They actually probably end up spending more money at the end because they don’t treat it. Guys who save a dollar end up spending twice as much later.”
Recovery’s income is mostly from pump sales, Keesee said, but pump maintenance and repairs keep him and his colleagues busy. Recovery works on different types above-ground oilfield pumps. In the realm of emergency service calls, nothing’s worse than a saltwater disposal well breakdown—at least when there’s no other way to handle the produced water, often the case for independent operators.
“When your injection well is down, your lease is off,” Keesee said. “We have two work trucks that go out in the field. We also bring them to the shop. It depends on what type of repair needs to be done.”
Keeping saltwater disposal wells running properly helps operators maintain good relationships with regulatory agencies—or at least avoid trouble.
Disposal wells are regulated regarding not only operation but also construction and location, primarily in the interest of protecting drinkable groundwater. In Texas, the Railroad Commission (RRC) enforces the regulations. In New Mexico, enforcement is also handled by the state. In some states, the U.S. Environmental Protection Agency (EPA) is the default regulatory agency. The Safe Drinking Water Act of 1974 comes into play.
On websites, the parlance differs between the RRC and the EPA. Under the heading “Saltwater Disposal Wells,” the Railroad Commission recognizes the various common names used in the oilfield for different types of disposal wells, describing three categories according to permits required for each:
Injection wells or secondary recovery/injection wells that allow the return of oil and gas produced wastewater to the reservoir from which it came in order to achieve enhanced or secondary oil recovery.
Disposal wells for the injection of produced wastewater into non-producing zones that are sealed above and below by impermeable strata that isolate them from useable groundwater.
Disposal wells for the injection of produced wastewater into the zone from which it came—however, not for the purpose of secondary recovery.
The EPA categorizes disposal wells as Class II wells, a category that encompasses all oil- and gas-related injection wells.
From the website www.epa.gov:
“Class II wells inject fluids associated with oil and natural gas production. Most of the injected fluid is salt water (brine), which is brought to the surface in the process of producing (extracting) oil and gas. In addition, brine and other fluids are injected to enhance (improve) oil and gas production.”
The EPA breaks down the Class II definition into three categories:
Enhanced recovery wells.
Disposal wells.
Hydrocarbon storage wells.
The third category primarily describes the storage wells that comprise the U. S. Strategic Petroleum Reserve—over a hundred wells that store oil in underground formations.
In the United States, more than two billion gallons of brine go into Class II wells every day—mostly in Texas, California, Oklahoma, and Kansas, according to EPA statistics.
The RRC breaks down the statistics for Texas, based on 2013 statistics:
More than 50,000 permitted oil and gas injection and disposal wells exist across the state; approximately 35,000 are active. Roughly 20 percent are disposal wells.
The number of disposal wells continues to increase. A report based on May 31, 2015, figures shows 36,121 injection/disposal wells.
Some disposal wells are created from existing wells. Others are drilled. Crawford describes the process in general terms, based on his experience with Bosque:
“Typically you go out and find a location. You get permits. You drill it out.”
Drilling a well specifically for disposal rather than using an existing well has advantages.
“You’re in control from the beginning design to the end completion,” Crawford said. “Some variables are unseen when you convert an existing well to disposal. Typically we develop our own.”
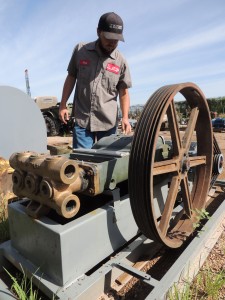
A refurbished 3364 Gaso-brand disposal well pump sits on a skid in the yard at Recovery Equipment in Abilene, ready to go back in the field. Touching the cast iron with a caring hand is Chad Keesee, operations manager. Partially visible to the left is the shield for the belt assembly. PHOTO BY HANABA MUNN WELCH
An option to trucking produced water to disposal wells is to transport the brine by pipeline.
“We do a lot of pipeline and gathering systems,” Crawford said. “More than 80 miles we have surveyed and constructed for operators. It increases the speed (of transport) and takes trucks off roads. The less trucks, the less the road damage. It’s beneficial for everybody. We make sure everything is up to EPA standards.”
Bosque prides itself on designing custom solutions for every water and fluid management challenge. All are different.
“It’s not a ‘one size fits all,’” Crawford said. “We’re very solution-based. We’re not just putting products out there.”
Recycling water is the new direction.
“It will be the future,” Crawford said. “We try to be as forward-thinking as possible.”
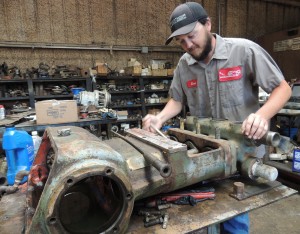
Wearing his shop shirt, Chad Keesee, Recovery Equipment operations manager, puts a wrench to a 3364 Gaso pump for a saltwater disposal well. Recovery, located in Abilene, sells new pumps and repairs old ones. Keeping saltwater disposal wells operational is a big part of the business. PHOTO BY HANABA MUNN WELCH
Crawford characterizes Bosque’s Clane LaCrosse, president, as a leader at the forefront of the ever-changing technological scene—someone who’s not just keeping up but also looking for better ways to do things, even amid the current slump cause by lower prices for oil. LaCross founded Bosque in 2007.
“We’re still hiring,” Crawford said. “We’re still producing new technologies and new product lines.”
Meanwhile, at Recovery Sales and Service, past and present prevail. It’s the nature of most small sales and service oilfield businesses. A few of the old pumps discarded in the yard are pieces of history—some brought in for impossible repairs and abandoned. If a saltwater pump can be rebuilt, Recovery tackles the task, making old equipment look almost new again. Even the new pumps sold are for conventional systems—the most cost-effective way to deal with saltwater in most places across the area served by Recovery. Keesee describes the territory as Knox County to the north, Menard to the south and Sweetwater and Colorado City to the west.
“We go anywhere they pay us to go,” he said.
But going onto a new lease and dealing with a new operator is the exception rather than the rule. Most customers have been dealing with Recovery for years and with owner Jerry Smith, Keesee’s uncle. When new people walk through the door, they’ve mostly learned about the business from an existing customer.
“The new people we do get, they say, ‘Hey, I was talking to so-and-so,’” Keesee said. “It’s more word of mouth. Your reputation means more than anything.”
It’s the rule of the oilfield, whether a company is big or small, building a new reputation or relying on an old one. Even saltwater disposal wells have a reputation. If they didn’t work, they wouldn’t be increasing in number every month in Texas even as recycling is emerging as a different way to handle saltwater.
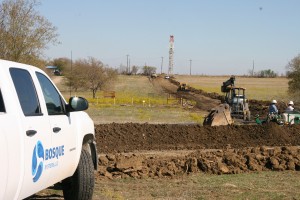
A pipeline project at Alvarado, Texas — now complete — shows one aspect of services offered by Bosque Systems, L.L.C. of Fort Worth. Bosque is a water management company that addresses a variety of needs in the oil and gas industry, including saltwater treatment and disposal. BOSQUE PHOTO
Disposal wells haven’t always existed. They came onto the scene in the 1930s. The EPA history timeline includes two entries for that decade:
The first documented project for the disposal of oil field brine (salt water produced along with oil and gas) into the originating formation began in Texas.
Enhancing the recovery of oil by injecting water or other fluids into a formation to extract additional oil and gas begins.
It was not until the 1950s that several states established regulations for the disposal of brine, according to the same timeline.
A report on oil activities in Kansas in the Dec. 17, 1937 issue of The Hutchinson News describes a classic disposal well:
Ohio Oil Company is drilling a salt water disposal well on the Decker lease in Graber field in South McPherson County. The company has 13 producing wells on this lease and some of them are making a considerable amount of salt water. The 13 wells are good for about 11,500 barrels a day of high grade crude from the Hunton Lime. They are to be allowed to produce 17,500 barrels of oil in the month of December. The disposal well is to be drilled to some horizon that will “take” the water and that also doesn’t make oil.
A story in the Feb. 20, 1938, Abilene (Texas) Reporter News tells about a producing well that became a disposal well and then a producing well again:
St. Mary’s Oil & Gas Company reported to the railroad commission Abilene district office this week that its salt water disposal well in the Moran field of southeastern Shackelford County is now an oil producer.
The company drilled its No. 4 R. L. Broadfoot, a shallow well in section 69-ROH survey, back in 1923 and it produced oil until last year. It was 640 feet deep.
On April 2, 1937, the company obtained a special permit from the commission to use the well for disposal of salt water produced in the pool.
In December, however, the well refused to take more of the salt water, the sand horizon apparently having been saturated.
St. Mary’s moved in a rig and deepened the old well to 697 feet on Feb. 8, discovering a second oil sand. With five-inch casing cemented at 495 feet, operators ran four-inch pipe inside and cemented it with five sacks above the second pay zone.
Placed on production gauge, the well pumped 35 barrels of oil and ten barrels of water. It showed 5,000 feet of gas and a pressure of ten pounds.
A story in the June 4, 1936 issue of The Ada (Oklahoma) Weekly News affords a look into deliberations and the parties involved in the establishment of a disposal well, including other options considered (no doubt, all non-compliant with today’s rules and regulations). The story concludes with a mention of pre-injection water treatment.
A well to put into instead of to take out of has been started a goodly distance northwest of the Fitts pool.
It is the first move in a “community” plan to get rid of salt water from producing oil wells in a way that will eliminate the troublesome problems of stream contamination.
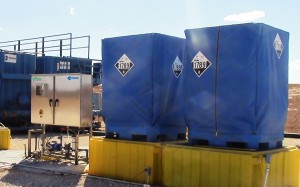
A Bosque System stationary water treatment unit serves a saltwater disposal well near San Angelo. Bosque’s proprietary system, DIONIX, also includes mobile units for treating water for hydraulic fracturing. BOSQUE PHOTO
The well is the No. 1 Hennigan, in the center of Section 8-2-6, and Friday it was drilling at 390 feet.
It will be taken to the Cromwell sand, which is to be the recipient of the salt water produced in the Fitts Field and which, to the oil industry, is a decidedly unwanted fluid.
Spread of the Fitts pool, the fact that some of the wells are already producing some water and the added fact that it is believed generally that eventually many more will as oil reserves are withdrawn, made the problem a big one and an immediate one.
Several schemes were suggested for disposing of the saline fluid, ranging from evaporation ponds to piping it over the hills to Canadian River.
But the operators, their engineers, and conservation department and conservation commission officials after earnest study decided on the plan of pumping the water into a sand where it cannot affect the oil bearing formations of the field.
The Hennigan well is the result. The plan will require a pipeline system to wells that have salt water ailing them, a central plant where bad oil and water will be treated and from which the treated oil will go into the pipelines and salt water will be pumped to the Hennigan well.
This method has been given several trials elsewhere with varying results, but with experience valuable to the Fitts field operators/
Porosity of the sand can be determined but some problems, as pressure required, remain to be worked out.
Treating of the salt water is necessary to remove solids that would contaminate the sand in the disposal well and by filling in the interstices block entrance of water into the bed of sand.
Freelance writer Hanaba Munn Welch writes regularly for PBOG. She maintains a website at www.hanaba.net.