With return on investment and environmental, societal, and governance (ROI and ESG) concerns topping the charts, service companies tasked with getting downhole and opening the wellbore are under the gun these days. Making hole quickly is the first step, and completing the well—or in some cases re-completing—can boost producers’ bottom line. Legacy Directional Drilling, GEOData, and Halliburton are responding to the push.
Legacy Directional Drilling, LLC, was founded in late 2014 and did its first jobs the succeeding year. The company focuses on MWD (measurement while drilling), motor optimization, well planning, geosteering, and other downhole services.
Company Vice President Mark Miller says he’s seen great leaps in drilling speeds, accuracy, and lengths over his career, which began in the 1980s. He and and Permian Sales Manager Andres Martinez joined in a phone interview for this story.
“We just TD’d [reached total depth required] a well in the Delaware past 26,000 feet,” Miller said. “I’m not saying that because that’s a record. That’s just what we do.” He continued, “If you think back, 26,000 feet in a horizontal section, 10 years ago, that was unheard-of.” Today those wells are just part of the job for the industry. “Customers expect you to get past 20,000 feet without even thinking about it.”
Martinez pointed out that it wasn’t too long ago that drilling a deep well in the Delaware Basin took 6 months or more. Now 20 days to TD is what operators expect, and usually get.
He said that doing long laterals that previously required just one bottom hole assembly (BHA) in the Delaware, common now, would have been unthinkable a few years ago. Even at half the length of today’s common holes, Miller added, it would have required 3-4 BHAs if it were possible at all.
Speed and Accuracy
What’s driving the higher speeds? Miller says it’s based on accurate MWD systems and reliable downhole motors like those they use from Gordon Technologies. It also involves using systems and motors appropriate for each formation and situation. “If you match it right,” said Miller, “you can almost make the formation negligible.” That has the effect of limiting downtime.
As to accuracy, geosteering takes the lead. “Almost all the wells we drill now are being geosteered,” said Miller, “where geologists are telling us what formation to stay in and what size window to stay in, to ensure the accuracy that the customer wants.” Azimuthal image gamma measurement accuracy is key to staying on course, Martinez said. “You can tell when you’re going up and down through bends, you can stay exactly where you want to be.”
The Back Story
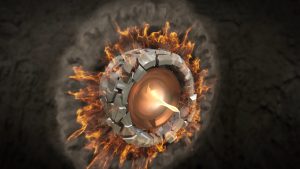
This Image is an artist’s conception of what a Connex [perforating] charge, by GEOdynamics, looks like when denotating downhole.
Nixing the idea of simply buying MWDs and motors on the open market and being “just the same as everybody else,” he said, “We decided that was probably not a real winning combination.”
It started with finding like-minded investors—from among family and friends—instead of Wall Street. The investors themselves, with guidance from Miller and associates on the business side, “went out and found an MWD system that was, we thought, second to none.” Here he referred to Gordon MWD. Because of their close working relationship, Legacy has access to assets not available to other companies.
Legacy also decided to rent motors instead of buying them. That way they could offer clients only the latest technology as soon as it hit the market, instead of trying to force-feed them the last of the old stock, whether it fit the purpose or not (something a previous employer of Miller had done). This has also allowed them to inform upgrades and changes by the manufacturer in motors Legacy uses, Martinez added.
New Shaped Charges from Big Red
Technology and procedures aren’t the only things changing in the oil patch. To keep up with those kinds of changes, testing and verification standards are also being updated, as with the American Petroleum Institute’s (API) protocols for testing deep-penetrating shaped charges used in completions.
Halliburton’s Stuart Wood, Strategic Business Manager for Wireline and Perforating, notes that the company’s new RockJet charges mainly incorporate incremental changes, although he expects increases in production of “many tens of percent.” The biggest excitement for RockJet’s developers is that it’s the first in the category to be witness-tested under the API’s new protocol.
These charges are used to open formations in production, saltwater disposal (SWD), and carbon capture and sequestration (CCS) wells. Their bullet shape focuses the charge jet to penetrate deeply into the formation, opening up pathways for flow in or out, depending on the well’s purpose.
Downhole, those charges blast through the cement layer but, of course, must also penetrate the rock to accomplish their purpose. Previous API standards, 19B API 19B (section 1), entitled “Recommended Practice for Evaluation of Well Perforators,” required only testing through cement. Wood noted that the problem there was that cement hardness varies by the mix, the thickness, and the season in which it was poured. It’s not a firm standard. It did not truly meet API’s stated goal for the test, of providing standard procedures for evaluating the performance of perforating equipment so that representations of this performance may be made to the industry under a standard practice.”
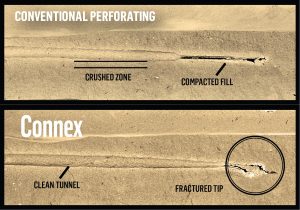
The Connex program, by Geodynamics, touts the superiority of clean tunnels and fractured tips-both achieved by GEOdynamics’s plug-and-perf technology.
New standards, under the added Section 2, require testing through stressed rock as found downhole, which gives “a much better idea of their expected inflow and outflow performance at real downhole conditions,” Wood said. The old assumption was, “if my charge can shoot longer in cement, it will shoot longer in rock. Our testing and analysis proves that is inaccurate.” The new standards took effect in mid-2021.
RockJet’s main application is for natural completions in large-bore offshore wells with gun systems of 4-1/2”, 4-5/8”, or 7” diameters. It’s useful in vertical wells, horizontal wells, and deviated wells.
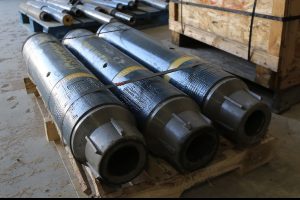
Legacy Directional utilizes the Shock Miser UBHO/Pulser Sub on every BHA. The Shock Miser has a built in “bi-directional” shock absorber that isolates the MWD tool from harmful axial (Z axis) shock and vibration.
Halliburton does plan to expand the reach of the RockJet in the future, “Our current plan is to continue this approach, including the witness testing, to build out the family of these rock-optimized charges” to work in everything from 2” gun systems up to 7”.” These are sizes that would be appropriate for land use including in the Permian Basin.
Released late in 2022, the RockJet has drawn interest from the industry already, Wood said. As real-world results begin to accumulate, Halliburton “expects production to be many, many tens of percent higher depending upon the scenario, especially if it’s in more challenging and harder rock, Wood said. “It can be calculated using inflow models such as Prosper, using the measured exit hole diameter and the hole geometry we’re getting from our Section 2 testing.” Exact productivity or injection gains will “depend a lot on the reservoir and the well details.”
Those improvements will come from the RockJet’s deeper formation penetration and a larger perforation tunnel diameter downhole.
GEODynamics Connex
Creating a clean perforation (perf) channel was the goal of GEODynamics Inc. in creating the Connex Clean Perforation Technology shaped charges, said Eric Marshall, PE. Marshall is the company’s senior technical advisor.
“The perforating process in general can force a lot of debris into the rock that’s being perforated,” he said. The blast penetrates the steel pipe and cement before reaching the formation. “Debris from the pipe and the cement and the gun’s charge itself can get plastered against the reservoir wall.” So the Connex is a reactive charge that creates a vacuum that pulls much of the debris back into the gun and out of the tunnel it created.
Marshall explained that a clean tunnel allows lower breakdown pressures and more consistency in stimulation results. “Where it really has an impact is in higher-permeability, more-conventional reservoirs that don’t need stimulation, they just need a really clean perforation tunnel.”
It’s also useful in refracs, where it penetrates through two sets of casing, and in SWDs. The double casing in refracs can create much more debris than a single layer does.
Noting that varying downhole situations call for different types of charges, he said, “I think of selecting a perforating charge almost like selecting tires for your car. There’s going to be an application for just about any scenario.” There aren’t radical differences in perf choices, though. He pointed out that each type of tire will basically get someone down the road, but some are better for the vehicle and travel type than others.
Getting the design to match performance is key. “We all know that paper and reality can be two completely different things sometimes. So our job is to make sure that what we think is happening in the design is as close as possible to downhole reality.”
Santo Petitto, the company’s sales manager for completion tools and perforating, added that Connex provides a long total depth of penetration versus conventional, deep penetrating charges and also creates a fractured tip in the formation, which can optimize perforating performance.
Permian Variations
Different tires for different formations comes fully into play in the Permian Basin, said Marshall. There “the rock is very heterogeneous, even from stage to stage. You have some pretty major stress contrasts, even in a horizontal well, where in theory it should be in the same reservoir, the same rock. The rock properties themselves still change pretty dramatically even over the course of a few hundred feet.”
Petitto said unconventional wells are not the only ones in the production world, although they dominate the market. He sees “a lot of work going on in the conventional route, where there’ll be a re-entry, perforation in a different zone, above an existing, area, and Connex really does have a good application there.” Most of the conventional work is offshore, but there are also options for the product in refracs onshore.
Paul Wiseman is a freelance energy writer. His email address is fittoprint414@gmail.com.